Are tubeless road tyres here to stay?
Love them or hate them - tubeless road tyres are getting better every year. So what exactly has changed?
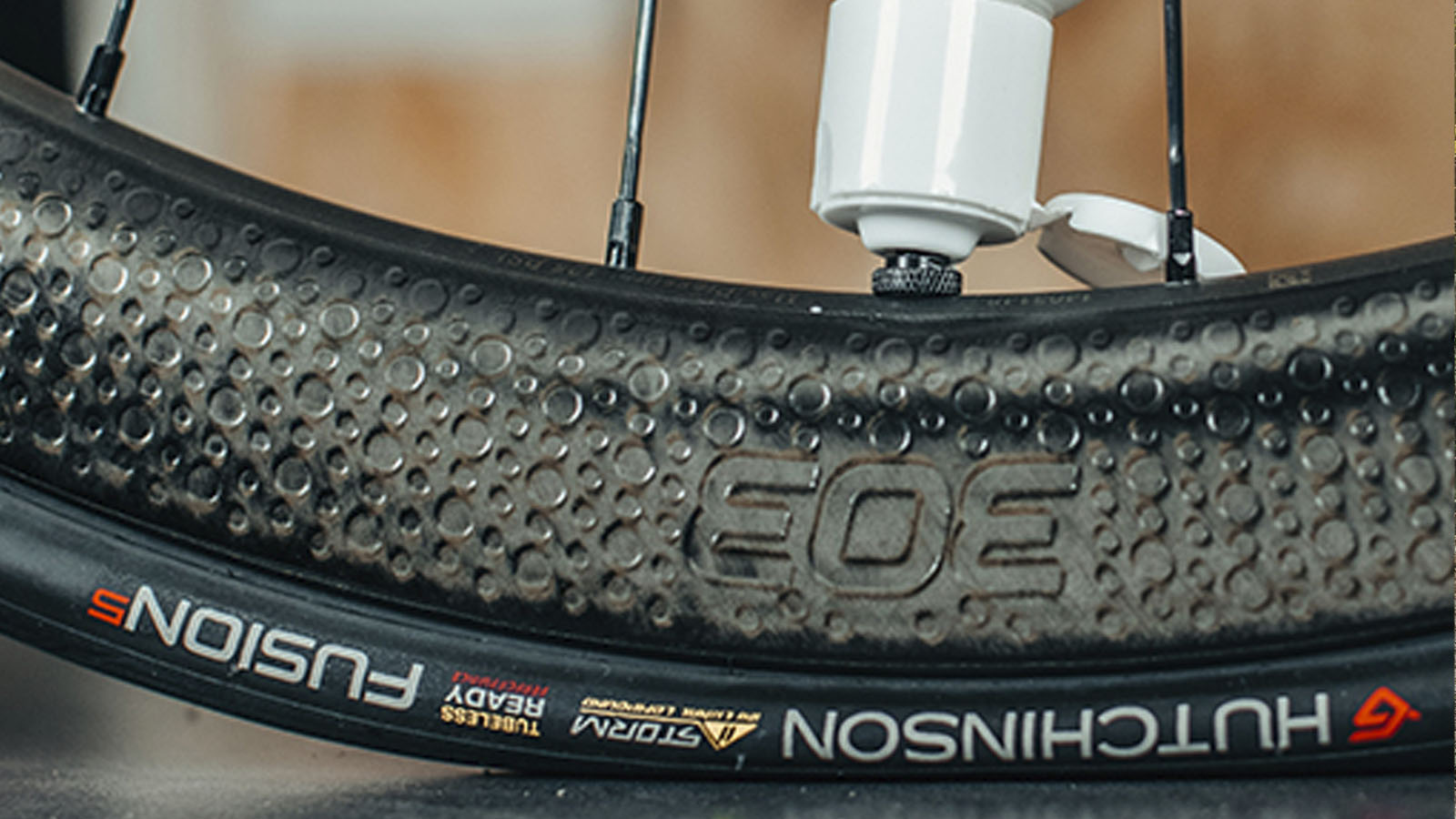
I still have vivid memories of the first time I used a set of the best tubeless road tyres, in this instance, it was Schwalbe's Ultremo tubeless. I had been running tubeless MTB tyres for some time, and the benefits in grip and self-sealing punctures had vastly improved my riding, so I attempted to sample the road-going skinny tyre version.
What I remember so vividly about this first experience of road tubeless wasn't how well they rode or the number of times sealant saved me from changing a flat - it was trying to get the damn things on my wheels and inflated in the first place.
That fateful evening when I skipped down to the garage with dreams of low tyre pressure, promises of less rolling resistance and the wonders of liquid sealant. Two hours, three broken tyre levers and one reprimand from an elderly neighbour to 'please stop swearing,' and I had only managed to get one tyre on the rim and holding air.
Fast forward a couple of years and I have set up numerous sets of road tubeless tyres from various brands. My cheap tyre levers from Aldi are still intact, the layer of dust collecting on my flash charger remains undisturbed and the only time I've uttered something remotely close to an expletive, was when my labrador puppy, Kevin, pranced by proudly carrying a Shimano S-Phyre shoe in his mouth.
It seems as though advances in tyre tech don't seem to garner the same level of hype as other components in the bike industry. Given that tyres are the best value for money upgrade to any bike, and tubeless road tyres can now be mounted with your thumbs and seated with a cheap floor pump, it's clear the R&D teams have been busy. But what's actually changed?
A bit like putting socks on a rooster
In the automotive world, tubeless tyre technology has been around since 1947 but the first instance of tubeless bike tyres came from Mavic with its UST (Universal Standard Tubeless) on the MTB side in 1999. It wasn't until 2006 that Shimano and Hutchinson paired up to release the very first road tubeless tyres. About six years later, we saw brands such as Schwalbe, Kenda, and Maxxis jump on board.
Ditching the tube brings with it no shortage of benefits on the road but it also means the tyre, specifically the sidewall and bead, have to do all the heavy lifting. Without an inner tube, it is incumbent on the tyre itself to create an airtight seal against the rim but, in the early days, this tightness served a dual purpose, also preventing it from blowing off the rim.
The latest race content, interviews, features, reviews and expert buying guides, direct to your inbox!
"The friction between the tube and the tyre sidewall creates a lot of stability. The force distribution of the tube in a tyre is focused mostly on the bead, which helps to prevent blow-offs. This is why you have almost no issues with blown off tyres using tubes," explains Schwalbe Product Manager Carl Kämper. "In our (early) testing, we noticed that tubeless tyres that were easier to fit were experiencing blow-offs, so we decided the best way to solve that at the time was to just reduce the inner tyre circumference; this is called the ITC."
A smaller inner circumference meant that even after the bead elongated during inflation, it still needed to stretch a considerable amount further to be dislodged from the rim. It also meant that the tyre was damn-near impossible to get on the rim in the first place, or as Kämper puts it, "it wasn't the tyre lever that bends the bead, it was the bead that bends the tyre lever."
It wasn’t just the smaller diameter that was bending the tyre lever, as Jöel Balez, a Research and Design Engineer at Hutchinson explained in an email, the bead itself needs to be stiffer, too.
"Compared to tube-type, the heel of a tubeless tyre is different — it has a slightly larger bead with a slightly different shape as well as additional rigidity compared to a tube-type bead as it will be subjected to more strain."
"Having an inner tube reduces the strain on the bead and therefore when there's no innertube, you need a more resistant bead (for the added constraints and pressure). When we talk about stiffness, it is equivalent to tensile strength (data we are able to measure in the laboratory).
The goal is to find a balance between the pressure on the bead and the ease of mounting," he says.
Whether we are talking about a wire or a folding bead, the bead itself consists of individual threads wound together to form what is essentially a string. Through the use of different materials and winding patterns, tyre brands can create specific characteristics — like high-pressure stability, stretch or stiffness.
The bead's exact makeup is a closely guarded trade secret but advancements in materials and manufacturing know-how have allowed tubeless tyre manufacturers to expand the ITC. Kämper tells Cyclingnews that the ITC of Schwalbe's tube-type and tubeless tyres is now almost identical with the only difference being core materials, and the new materials used in the bead allow for this without the risk of blow-offs.
To that end, he tells us that Schwalbe tests all of its tyres to 1.6x the maximum stated tyre pressure on the sidewall and, in the lab, one of its road tubeless tyres lasted an hour at 21bar / 304psi.
Hutchinson puts its tyres through a similar gauntlet. "We work on wheels that are at the minimum threshold of ETRTO tolerances as well as those at the maximum: this way we can be sure that the tyre is sufficiently tight to withstand a value of 150% the [maximum] pressure on small wheels as well as ensuring the largest wheels are also safe. Obviously, the bead should be easy to mount on larger wheels," Balez says.
"With the right materials and the right bead diameter, we can strike this balance,” he continues.
No compressor required
Once you have wrestled the tyre onto the rim, the next hurdle is getting the sucker to hold air. There is no shortage of tricks and tips out there as to how best to coax those high-tech tyre beads to snap into place, but in the early days, the most reliable method was to use an air compressor or a homemade flash charger — usually made from a two-litre soda bottle — and a soapy sponge.
Nowadays we are flush with all manner of high-volume floor pumps and flash chargers — which often cost almost as much if not more than a small air compressor — but these are quickly becoming less and less of a necessity because tyre brands have been hard at work to make their tyres easier to seat.
"Back in the day, you just needed pure force and a lot of airflow to get the tyre seated. So we started thinking about sealing the tyre before it was seated on the rim," Kämper says.
The solution, as Kämper explains, was to add a small lip of rubber to the heel of the bead. It’s only a few millimetres of extra material but is enough to push up against the sides of the centre channel and create an airtight seal, eliminating the need for that initial blast from a compressor. Schwalbe isn’t the only brand using this line of thought, the Dual Angle Bead found on Goodyear's Eagle F1 Tubeless Complete tyres is a similar concept.
Pro tip: if you're struggling to get a tubeless tyre to seat, remove the valve core. If you're still having trouble, Kämper says that you can remove the pump head and place the hose directly on the valve for ultimate airflow with some pumps.
Rim shape is key
Earlier, we broached the topic of rim shape and ETRTO (European Tyre and Rim Technical Organisation) tolerances. These are essentially the dimensions that wheel manufacturers are supposed to design their rims to fit within. It is the variance in these tolerances that causes poor rim and tyre combos.
"The rim plays a very, very important role. In our daily work, we must rely on ETRTO profiles, which set the standard. However, not all rim manufacturers rely on these standards. The more that rim manufacturers deviate from these recommendations, the more likely we are to have unpleasant surprises when combining a tyre that meets the standards and yet a rim that does not meet them (whether in installation, security, low-pressure leaks, etc.)
"The tyre/rim combo is an important pairing. If one breaks the rules it causes an imbalance, which means that nothing can work properly," explains Balez.
Kämper tells us that Schwalbe has even gone as far as contacting every wheel manufacturer and requesting rims to be measured in their lab in an effort to establish how well they work together and create a compatibility chart. Schwalbe is far from the only brand conducting this type of testing; other tyre manufacturers like Hutchinson, Specialized and WTB, and rim manufacturers such as ENVE, Giant, Zipp and others, offer compatibility charts on its websites.
"If the rim well is too narrow or not deep enough, you will have mounting issues, or if it's too deep, the tyre will not come out, so there is a sweet spot for that, too. For mountain bike tyres, the width of the shoulder segment is crucial to prevent burping. Burping really comes down to rim design; the more narrow the shoulder of the rim, the more of an issue you have because there is no play for movement as the tyre flexes," he says.
"Quite often, when manufacturers will re-design a rim, they will reach out to ask for design advice for maximum compatibility with our tyres," Kämper explains. “We have put a ton of work into tyre development but also rim manufacturers have put a lot of work into getting their dimensions right and stable to stay within the ETRTO dimensions so everything will work nicely.”
WorldTour teams have been experimenting with tubeless tyres (and winning Tour de France stages on them), which, backed by third-party rolling resistance data, makes it hard to argue with the performance advantage available. With the tyres themselves approaching weight parity with their tube type counterparts, the final hurdle for tubeless to overcome will be usability.
No matter how you slice it, tubeless tyres are a bit more difficult to set up and maintain than their tube type compatriots; there is a specific technique for mounting the tyre, the sealant needs to be refreshed at semi-regular intervals, and they can be more challenging to get inflated than an inner tube. The difficulty gap has come down considerably, but there is still a learning curve with tubeless.
Given that tubeless road tyres have been on the market for nearly 20 years, it’s hard to see them ever becoming the norm as they are in the MTB and gravel arenas. For the time being though, for those that have made the leap, they sure do ride nice.
Based on the Gold Coast of Australia, Colin has written tech content for cycling publication for a decade. With hundreds of buyer's guides, reviews and how-tos published in Bike Radar, Cyclingnews, Bike Perfect and Cycling Weekly, as well as in numerous publications dedicated to his other passion, skiing.
Colin was a key contributor to Cyclingnews between 2019 and 2021, during which time he helped build the site's tech coverage from the ground up. Nowadays he works full-time as the news and content editor of Flow MTB magazine.