Torque wrenches: Why you need one and how to use them
Get one now or potentially pay the consequences later
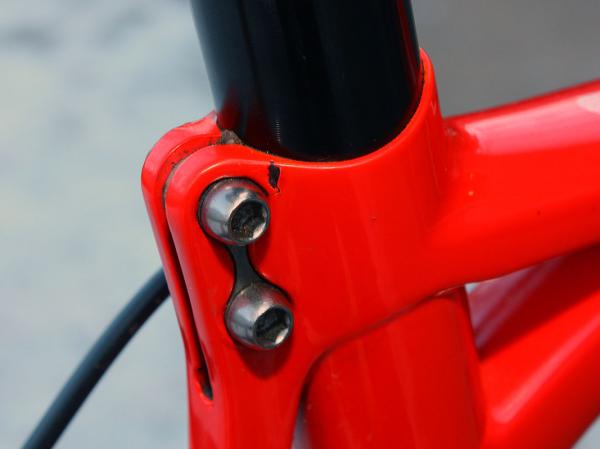
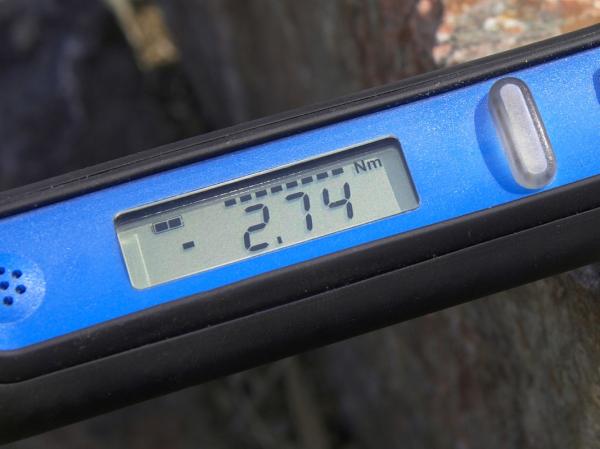
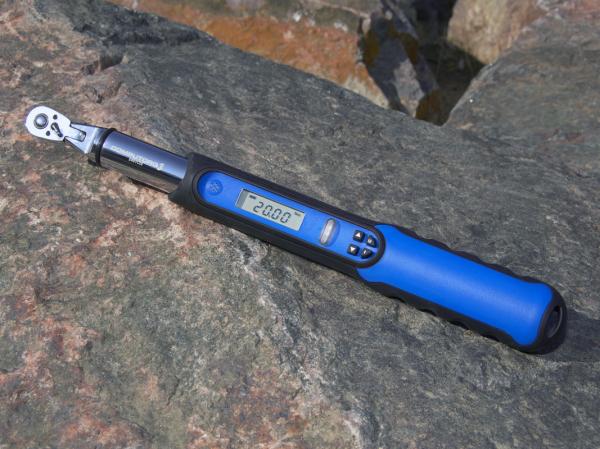
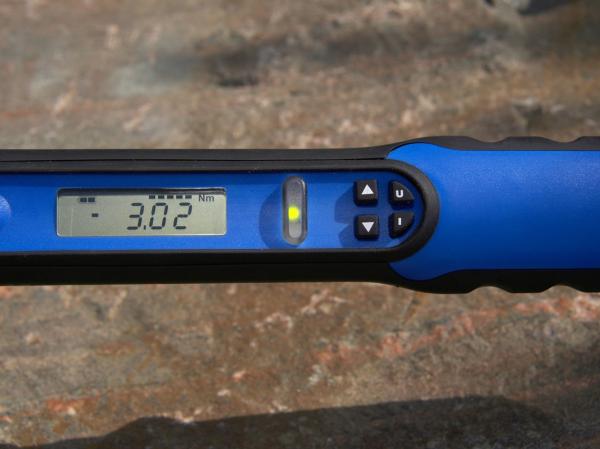
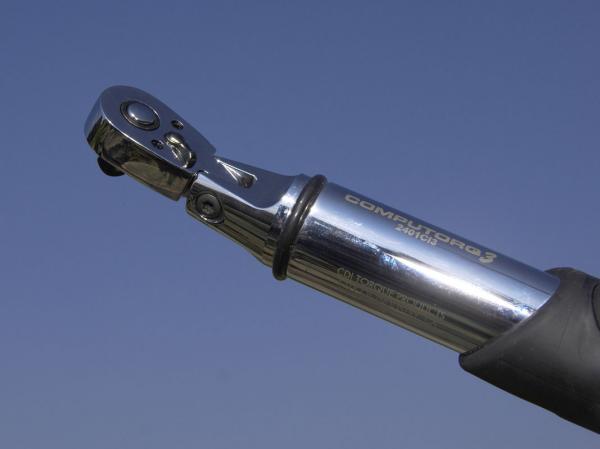
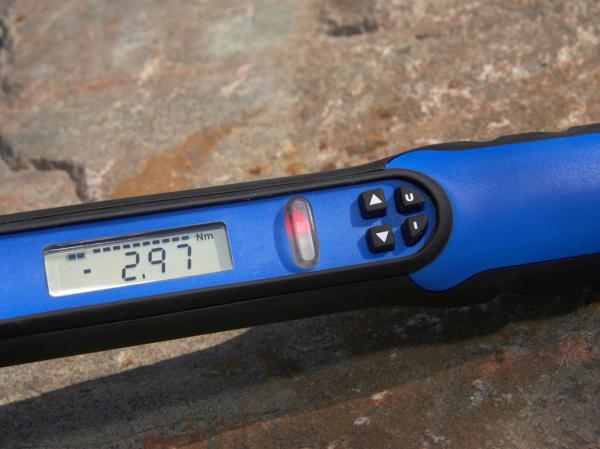
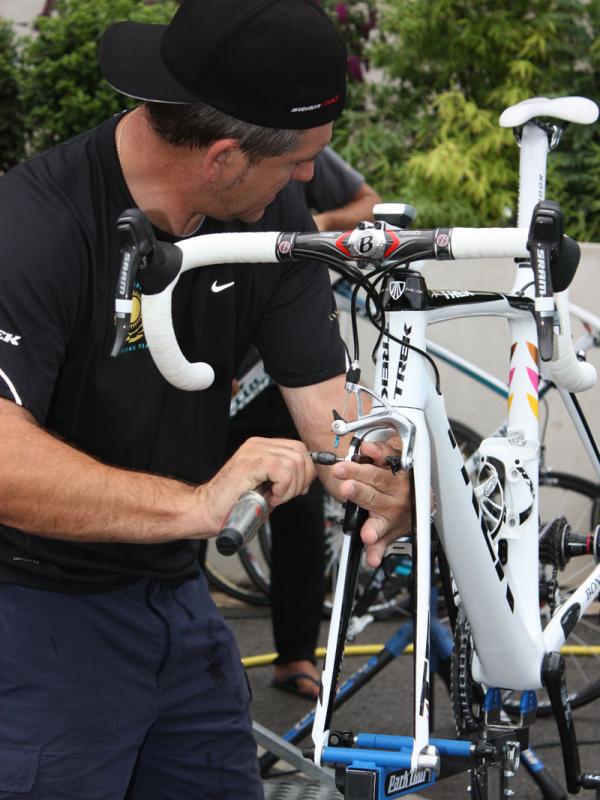
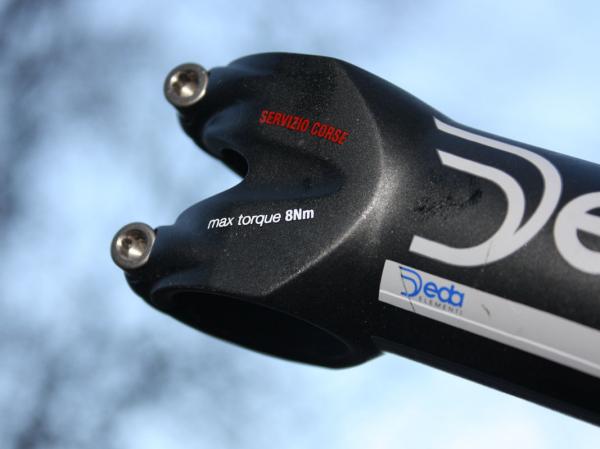
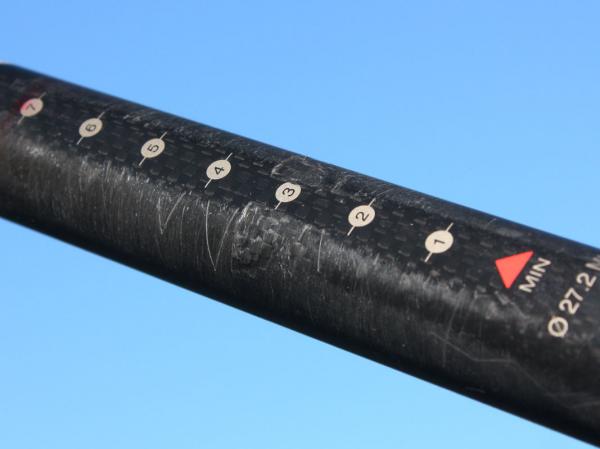
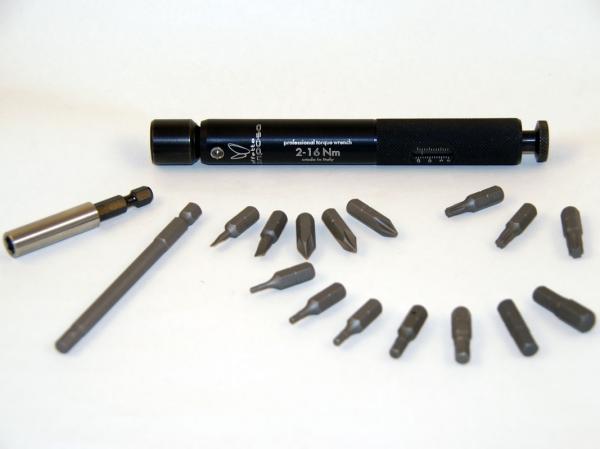
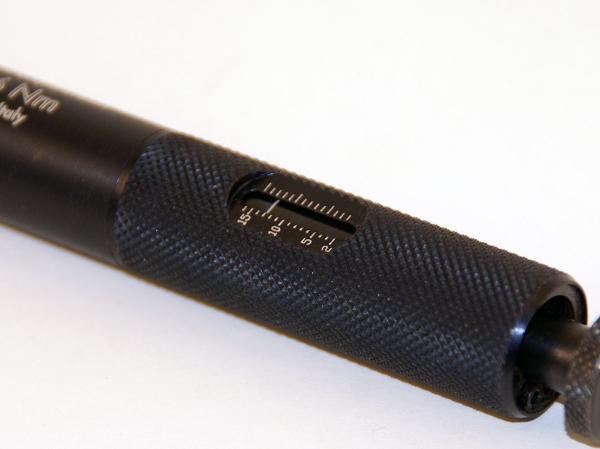
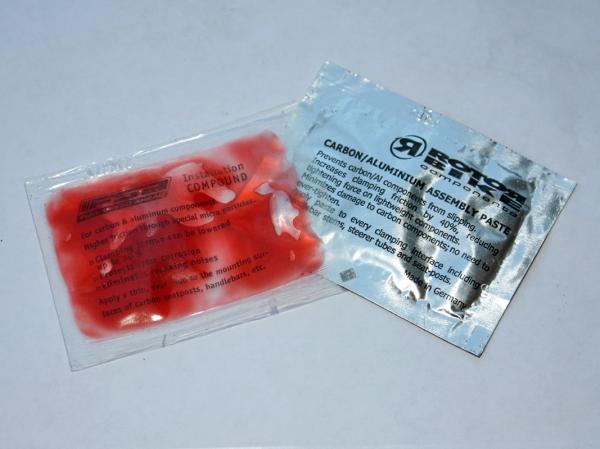
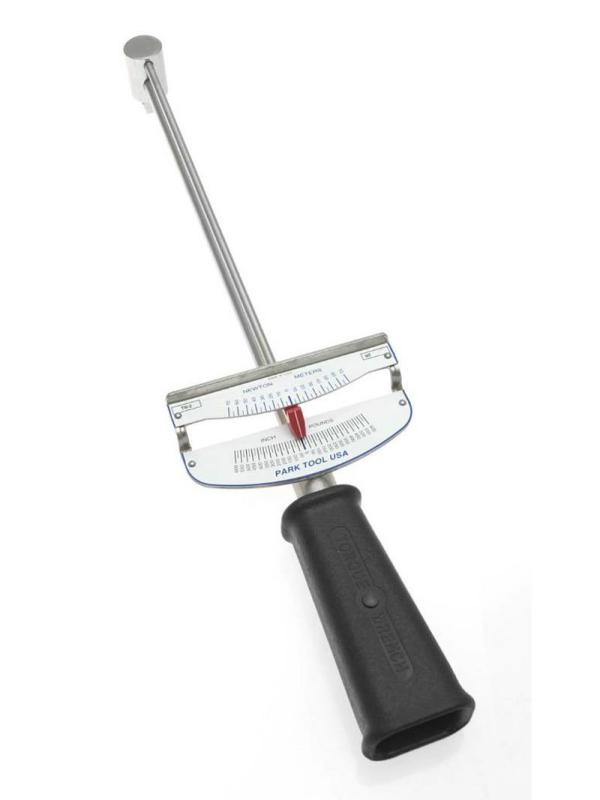

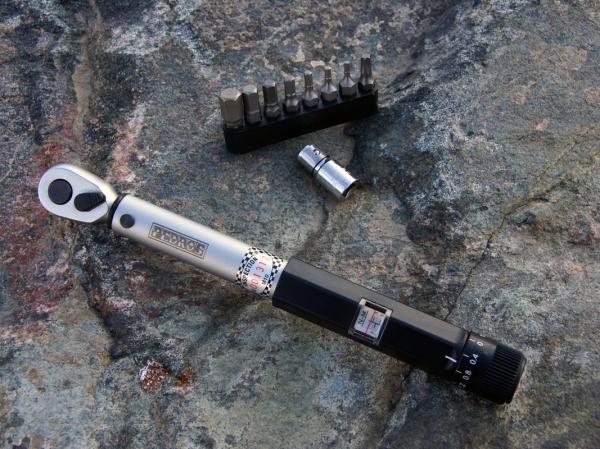
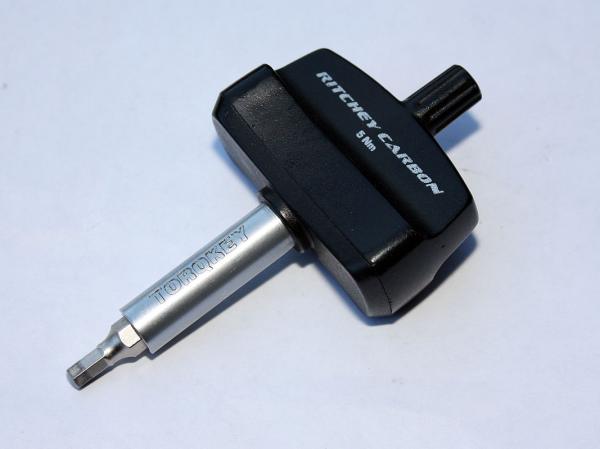
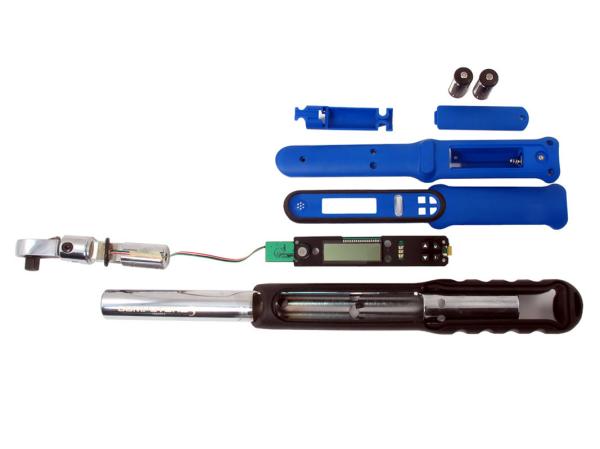

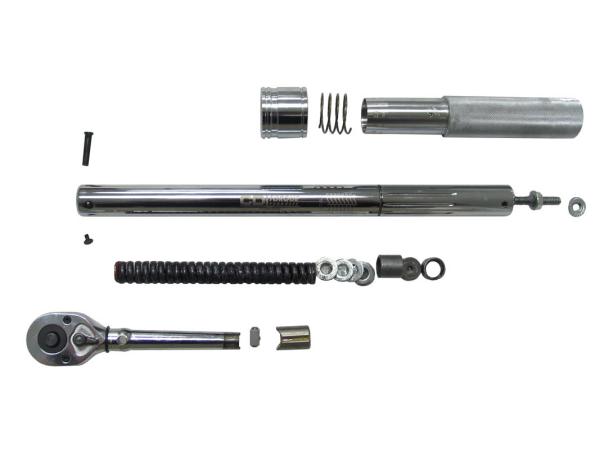
Torque wrenches were once considered an optional luxury, even in better bike shops. But more aggressive advances in bicycle frame and componentry technology now require stringent handling in terms of service and maintenance and even the most finely calibrated 'mechanic's feel' can't substitute for the real thing. Consider yourself warned...
Today's high-end parts are lighter, stiffer, often stronger, and definitely more expensive, and yet simultaneously more delicate as they’re increasingly engineered to fulfill very specific functional requirements and little more. As you, the market, continually demand more efficient uses of material, designers must prescribe more narrowly defined requirements in how those bits are installed and serviced. Whereas back in the day we used to see snapped bolts and stripped threads, it's become increasingly common to see cracked parts and broken bikes instead – the fasteners are no longer the weak link like they used to be.
"Products of the past were limited in their design by the manufacturing technology that was available to make them rather than the loads the products would see in use," says Garrett Smith, engineer manager for SRAM's California development center and former stress analyst for Lockheed Martin Astronautics (in other words, a bona fide rocket scientist). "Engineers could only make tubes so thin, or forgings so complex, because of manufacturing constraints. So you could say that the strength of the part was driven by manufacturing rather than use. But modern manufacturing technology is no longer the constraint that limits how thin a tube can be; the limit is now being driven by the loads the product actually experiences in the field."
"The design of our frames and components is always oriented towards lightweight," adds Scott engineer Benoit Grelier. "Thanks to our experience and FEM analysis, we can optimize precisely all wall thicknesses and we can use different materials, depending on the forces involved. But this also implies that we have less margin for the tightening torques."
The proliferation of carbon fiber in cycling stresses the importance of proper torque even further.
"While torque specifications are important with all type of materials, the growing number of carbon fiber components has led to an increasing focus on torque specifications," says Pedro's engineer Jay Seiter. "While carbon fiber allows for more optimal design and provides a far higher strength to weight ratio compared to steel and aluminum, it is also more susceptible to crushing and cracking when improperly set up."
Interestingly enough, torque isn't even the thing engineers and designers really care about – it's merely the most readily accessible indicator of the tension in the fastener, and subsequently the amount of force applied to the parts that are clamped or otherwise held together. With that being said, knowledge of what those forces are supposed to be is exactly what is allowing the industry to push the envelope on equipment weights.
The latest race content, interviews, features, reviews and expert buying guides, direct to your inbox!
See those little torque markings on your parts? Use them.
Automotive mechanics generally have to resort to extensive reference manuals to determine the proper torque spec on a particular fastener but we're much luckier – most critical parts now have the specifications etched or marked right on them so there's little chance for error. That is, assuming you pay them heed.
A spec of 5Nm doesn't mean 'snug' and 15Nm doesn't translate as 'tight' and regardless of what you may believe, so-called 'mechanic's feel' can at best only provide a close approximation of reality. Even the most finely calibrated hands are still both imprecise and inconsistent, varying by the day, mood, and routine of their owner.
"Having and developing a correct 'feel' when tightening fasteners is still important to the professional mechanic; there are many cases where the part cannot be fitted with a socket, or a torque wrench is simply not available," says Park Tool resident guru Calvin Jones. "[But] I have seen people be off a torque spec by as much as 50 percent, either too loose or too tight. Mechanics, like the entire human race, are susceptible to habit. As a rule, untrained people tend to under tighten the higher torque values, and then over tighten the lower torques.
"Given a limited number of steel fasteners, a mechanic might learn by trial and error, by failure, how much to load a thread," he continues. "Now throw in aluminum threads, carbon parts, magnesium, and titanium, where the feel and even the desired loads are different, and you are asking for trouble."
Studies conducted by torque industry specialist J.H. Williams Tool Group/CDI Torque Products (a division of Snap-On) yield similar conclusions, using a more high-tech test apparatus that accurately measures actual applied torque on a load cell in relation to what the subject thinks he's applying.
"At Interbike [2008], we had a transducer set-up to a ¼” breaker bar and hex bit socket and we asked for volunteers to tighten the bolts at the stem/steerer to the recommended torque value [4.5Nm – a common spec for those types of parts]," said marketing product manager Glenn Kalnins. "Of the nine volunteers, only one person was within spec (+/- 4%) of the 4.5Nm value [and] some people pulled five and six times the value that was set on our clicker. Imagine your stem faceplate needs to be tightened to 5Nm to hold your brand new carbon bar in place and you or your local mechanic tightens it to 25Nm or 30Nm. This variability is totally unacceptable in terms of safety and liability in the bicycle industry."
Given that quoted safety factors in some high-end parts can be as low as 1.1 (meaning that exceeding the spec by just 10 percent can result in failure), it doesn't take much of a ham-fisted mechanic to do some real damage. Conversely, the narrow window also means it's easy to leave a bolt too loose, resulting in unwanted movement or slip.
Torque wrench types – some are better than others but almost any of them are better than none at all
Torque wrenches remove the guesswork from tightening fasteners and their wide range of available types and costs mean that integrating one into your home toolbox is now easier than ever – and strongly recommended if you couldn't tell by now.
So-called 'clicker' wrenches such as the Park TW-5 and TW-6, Pedro's Demi-Torque, Effetto Mariposa Giustaforza, and Syntace Torque Tool (starting at around US$90) are the most common and readily available, operating via an internal spring mechanism that gives way when the desired torque is achieved. Both fixed-torque and adjustable models are currently on the market, and Kalnins stresses the 'sweet spot' for adjustable models is between 30-80 percent of the calibrated range. For more specific applications, small fixed-setting tools such as Ritchey's Torque Key can be had for as little as around US$20.
Proper usage and tool care is essential, though. According to Kalnins, the most common errors are continuing to apply force after the 'click' or applying torque too quickly (which can lead to overshooting the target), holding the wrench incorrectly (he says to always use the designated handle), or putting the tool away in anything other than its lowest torque setting (which can affect the calibration). Used correctly and adequately maintained, though, and clickers' claimed accuracy of around +/-5 percent should suffice for most applications.
Home mechanics on a budget can still find reasonable accuracy in a simple 'bending beam' type of torque wrench such as Park's TW-1 and TW-2, which often sell for as little as US$40. Completely devoid of mechanical joints, these simply operate on the principle of calibrated flex: simply insert the tool bit into the fastener, hold the handle, and apply torque until the indicator needle moves to the desired value.
Though generally inexpensive, bending beam wrenches are prone to damage if improperly stored (the needle is often exposed) and improper readings can result if the user isn't looking straight on at the gauge. In addition, they're often quite big and cumbersome and ill suited for portable use.
For well-heeled mechanics, the ultimate torque wrench is a digital type such as CDI's Computorq3, which offers a +/-2 percent claimed accuracy by foregoing mechanical devices for a solid-state electronic force transducer. Most models include an easy-to-read (and interpret) LCD display that readily converts between various units, too, and in the case of the Computorq3, a three-stage LED and audible tone also warns users when the preset torque is near. Even more useful, however, is that it also stores the actual applied torque, which also serves double-duty to train mechanics on proper usage.
That extra functionality comes at a high price, though. Suggested retail price on the Computorq3 is between US$325-350.
Other notes
Fastener and part conditions can drastically affect torque readings – and the more important actual bolt tension – so be sure to follow indications provided by the component, not the tool, manufacturer. Should the bolt be greased or should threadlock be applied? What if the bolt is rusty? All of these factors can affect the reading and not always in the direction of prudence.
Likewise, clicker-type wrenches should be periodically calibrated for optimum accuracy as values can drift over time. Kalnins also recommends that buyers stick to wrenches that include a calibration certificate from a qualified third party, such as the National Institute of Standards and Technology (NIST) in the US or equivalent. However, even a slightly out-of-calibration torque wrench will still almost certainly boast better accuracy than your bare hands.
The consequences for failure
US$500 for a torque wrench is an awful lot of money for most users but even so, it can be a small price to pay as compared to the cost of failure. Take BMC's Pro Machine SLC01, for example, which uses a carbon fiber seatpost clamp integrated into the frame structure. The torque spec on the lower bolt is just 8Nm and 5Nm on the upper – exceed either of those values by too much and you've basically got yourself a US$3000 trainer bike. That's an extreme example for sure though also one we've witnessed firsthand (a little too firsthand, in fact).
Other failures can be far less expensive but more catastrophic: carbon bars can break during a sprint, steerer tubes can crack, cranks can come completely undone. In more fortunate situations, improperly torqued parts will fail during servicing instead of while on a ride, or items will simply loosen up without causing a crash. In any event, the potentially negative effects can range from merely inconvenient to much, much worse.
From a technology standpoint, though, consumers' more rigorous adherence to torque standards may allow designers to build ever lighter and higher-performance bits in the future.
"If stricter torque values are adhered to, products can be made lighter and lighter yet keep all the required strength," says FSA technical support manager Dae Oh. "Currently, a lot of the overbuilding of products is to survive improper installation."
In other words, proper torque can mean safer and more hassle-free riding, cost savings in the long run, and lighter and more reliable parts for all of us. Sounds like a win-win to us.