NAHBS 2013: Kirk Pacenti's eecranks
Rebirth of Sweet Wings
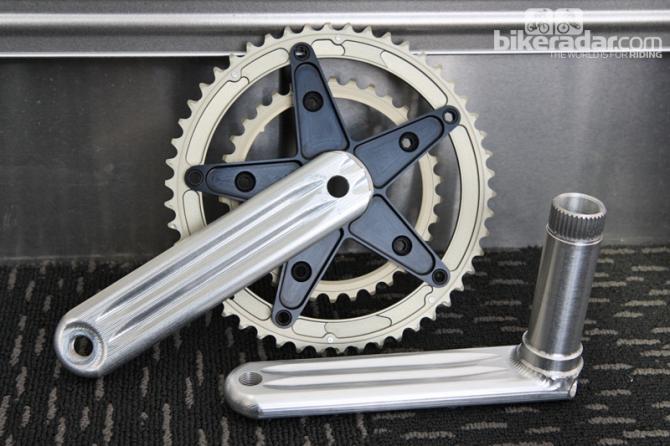
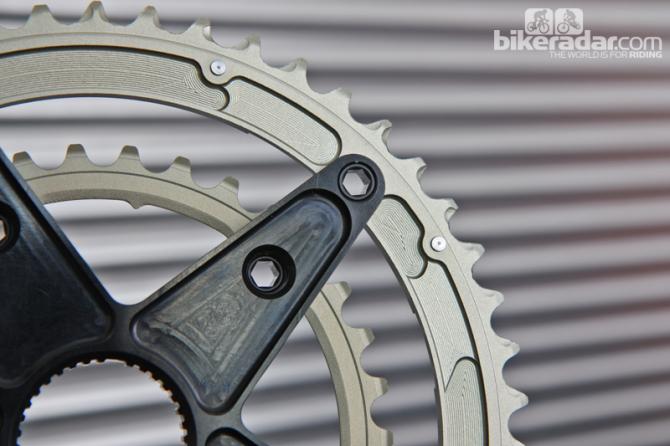
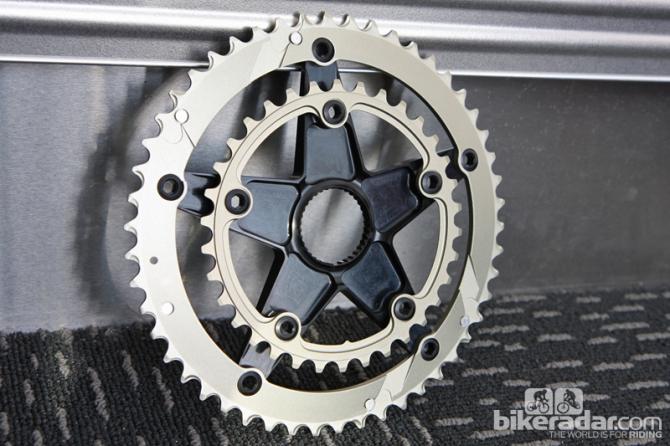
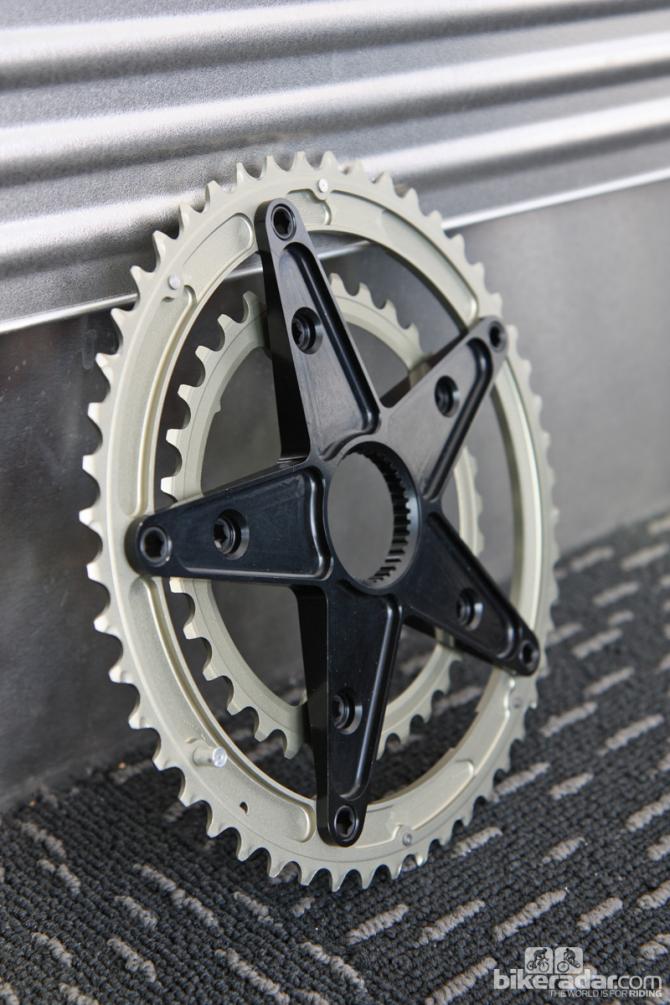
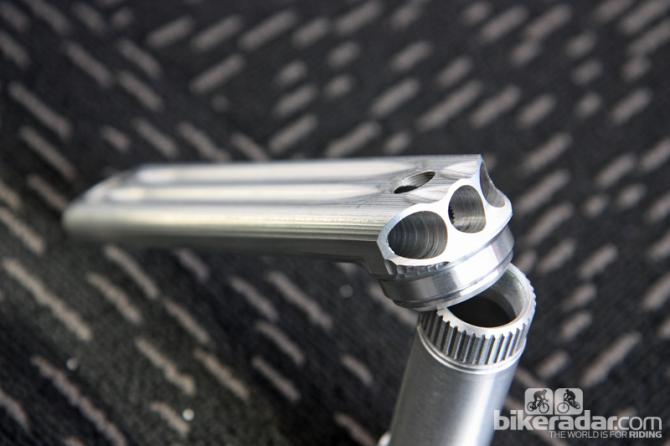
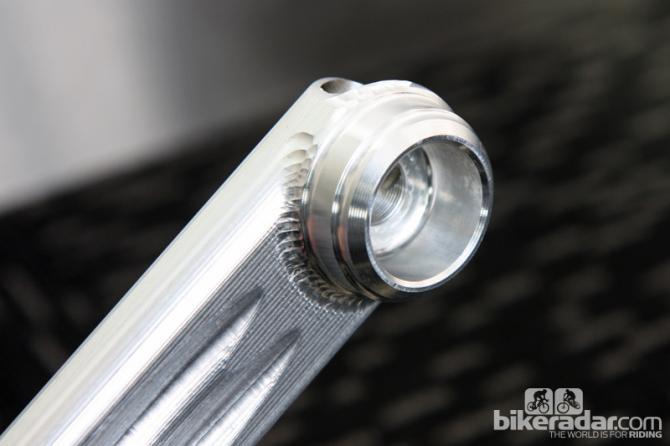
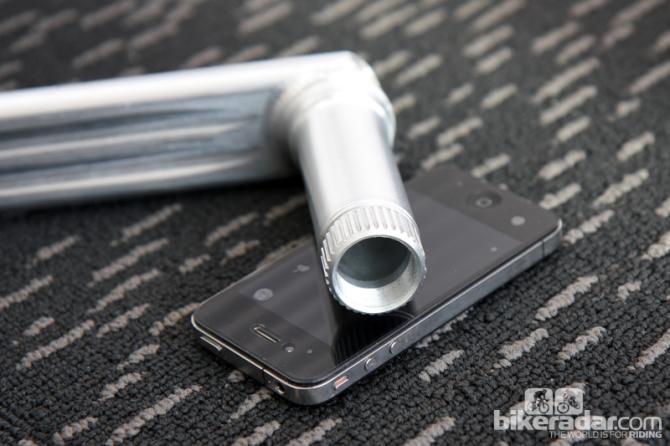
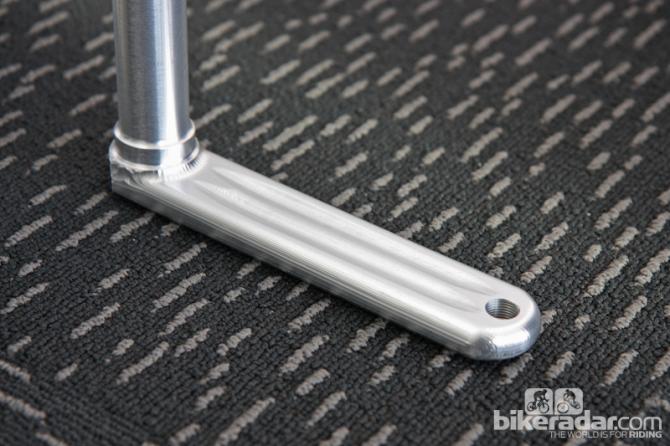
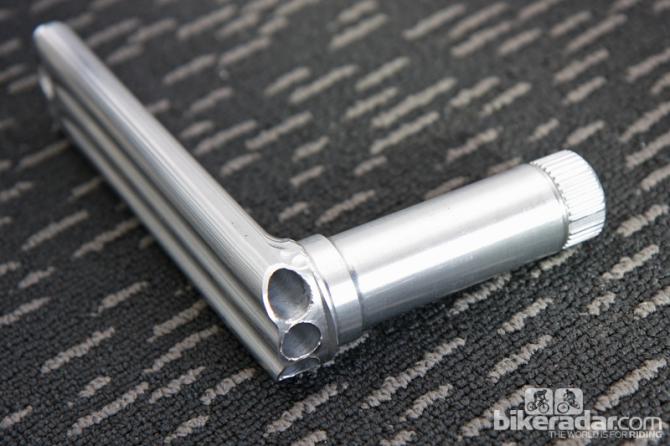
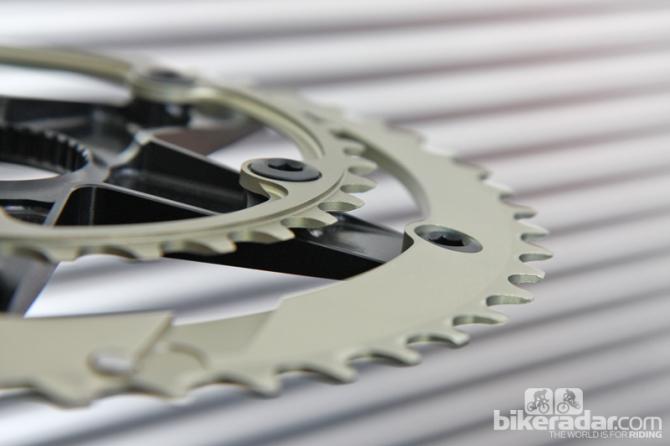
This article originally published on BikeRadar
After years of work supplying frame builders with his BikeLugs.com business, 650b pioneer Kirk Pacenti is now expanding his focus to components, starting with taking over the manufacturing and final design on Craig Edwards' long awaited eecranks – the modern machined aluminum rebirth of his old chromoly Sweet Wings. BikeRadar got an exclusive hands-on look at some near-production samples at the North American Handmade Bicycle Show.
The eecranks may not be as gracefully sculpted as some other high-end cranks on the market but that's because Edwards' design is so engineering driven. The deep-profile arms are triple-drilled to effectively yield a hollow arm with double rib reinforcements, the outer surfaces are channeled to shave more weight, and the non-driveside arm and massive 32mm-diameter spindle (expanding to 35mm at the bearings) are machined from a single chunk of billet.
The I-beam-profile spider is machined from aluminum as well and uses a proprietary 170/110mm bolt circle diameter to provide more reinforcement for the chainrings than traditional setups.
The numbers back up the unusual-looking design, too: right around 610g for the complete set including bottom bracket and chainrings, absolute stiffness figures that are supposedly surpassed only by Shimano's latest Dura-Ace model, and a big $850 price tag.
In addition to what we expect to be outstanding chainring stiffness given the massive spider, Pacenti says the tooth profile and pin designs have been engineered by the folks at Praxis so we anticipate excellent shift performance, too.
The external-type bottom bracket design is similar in concept to SRAM's GXP. One of the inner races – the driveside one, in this case – is sandwiched between a shoulder on the bottom bracket and the self-extracting crankarm while the other bearing can float axially on the spindle. Wave washers or micro-shims will accommodate shell widths that are out of spec (we're hoping for micro-shims).
The latest race content, interviews, features, reviews and expert buying guides, direct to your inbox!
"Even I think, 'gosh, that's so inelegant', but it's not a design flaw with the crank," said Pacenti. "It's a tolerance issue with the bottom bracket [shell]."
For now, Pacenti will offer the cranks only for threaded and PressFit30 bottom bracket shells. The current design definitely won't work, however, with BB386 EVO, BBright, Shimano's PF86, or Trek's BB90/95 shells.
"Right we've got our hands full and those are all ready. We've got a hundred sets of each of those and we know we can do that. Once we start selling things and we see what people start asking for and we actually start generating some revenue to do more development – if there's something we really need to address, we'll do it."
Pacenti also plans to eventually move away from machining raw billets to forged-and-machined construction. While that will theoretically improve fatigue strength even more than current test samples (Pacenti says the cranks are easily surpassing EN standards), the major improvement will be an estimated 80 percent reduction in machining time.
There's also the issue of the name. While many will likely always see these as a Craig Edwards – and thus, "ee" – design, Pacenti has purchased the intellectual property from Edwards and ultimately the cranks will be Pacenti-branded.
Either way, we're looking forward to getting our hands on a set for testing and Pacenti has promised BikeRadar an exclusive at the first set for media, too.
Final production is set for the next few of weeks so check back soon.
The triple-bored crankarm