Pro bike: Tyler Wren's Boo Bicycles BooCX
A composite of composites
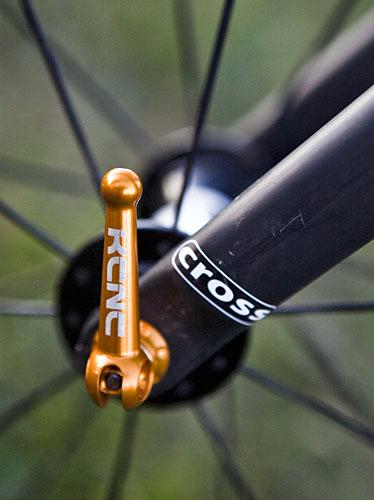
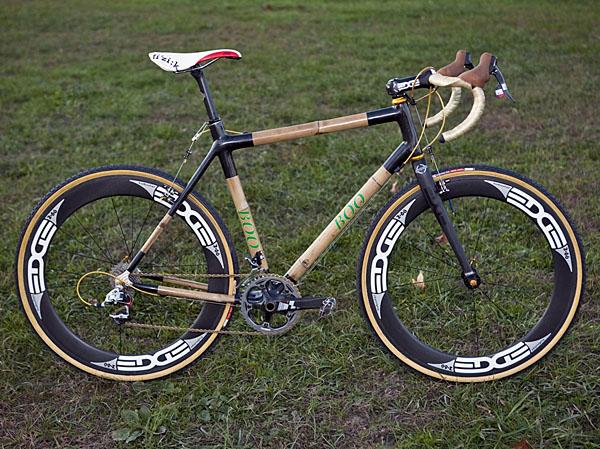
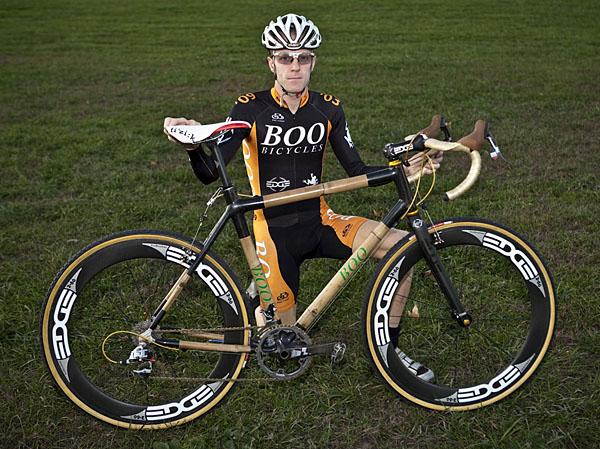
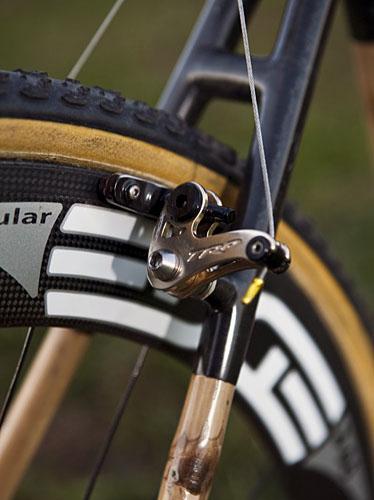
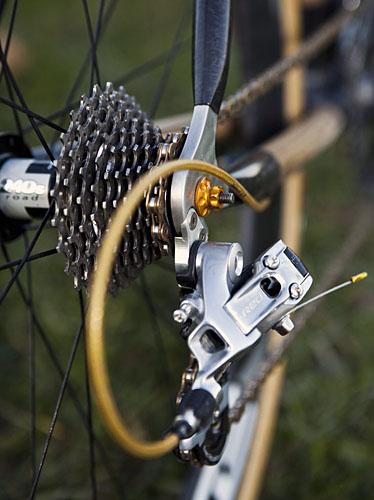
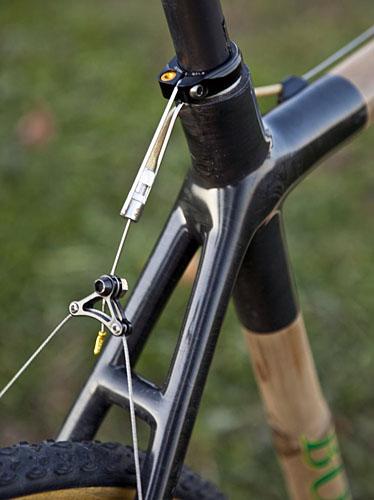
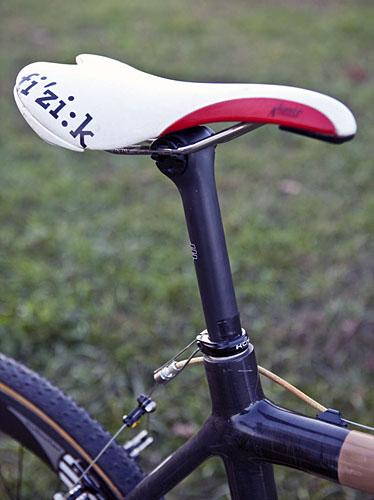
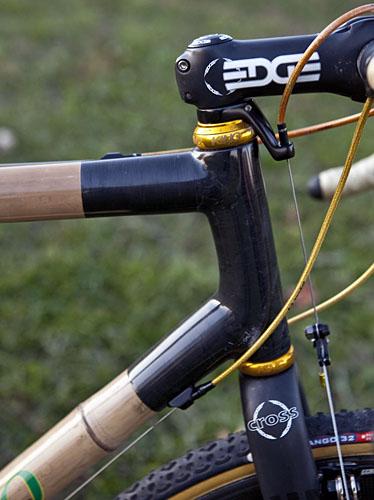
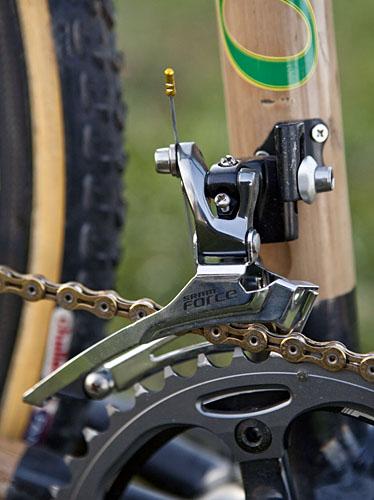
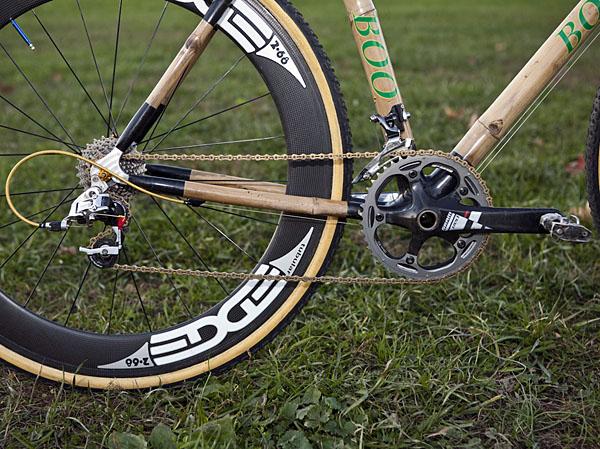
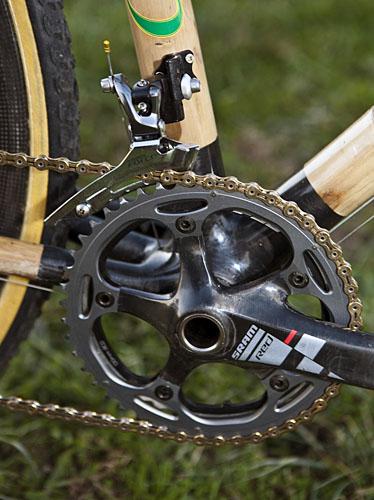
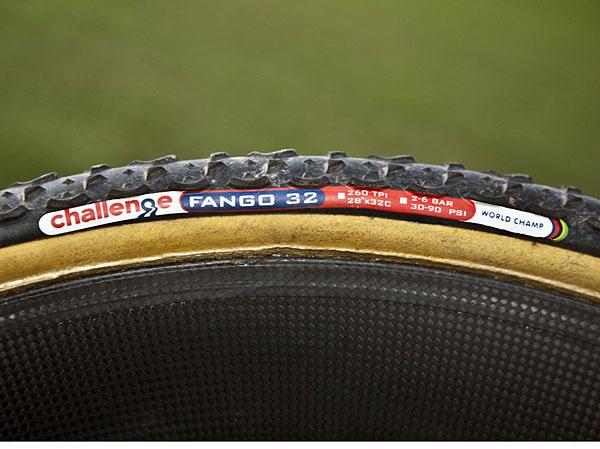
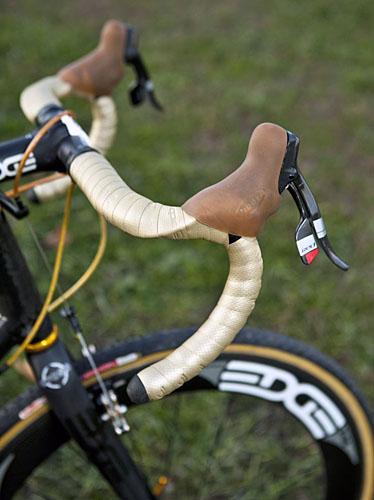
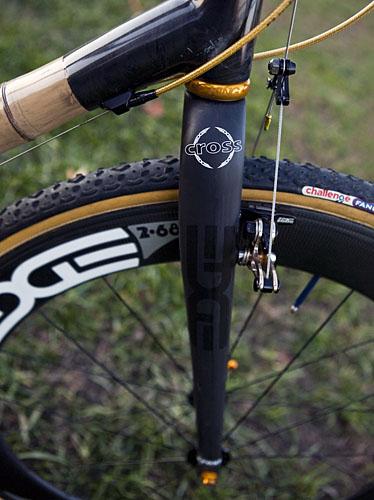
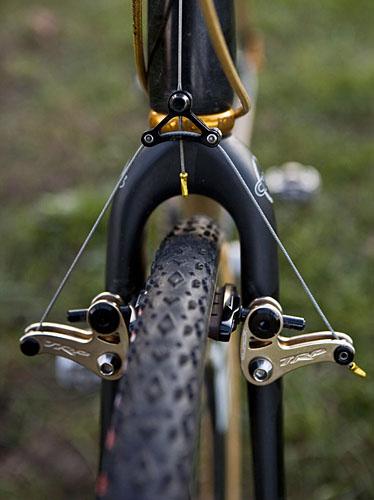
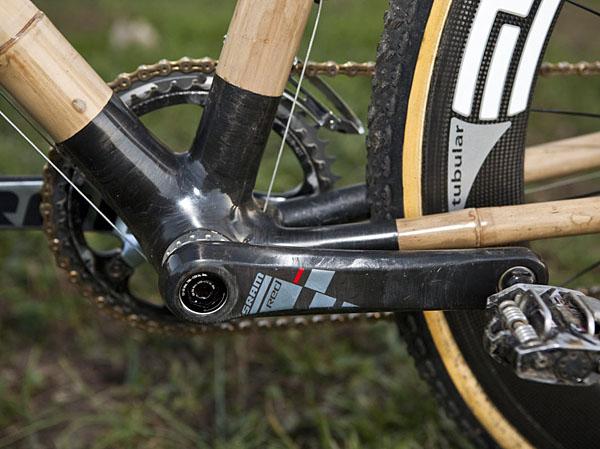
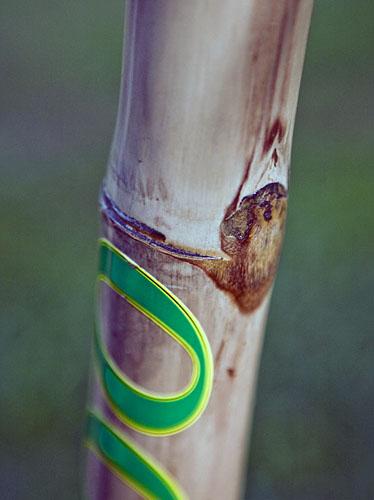
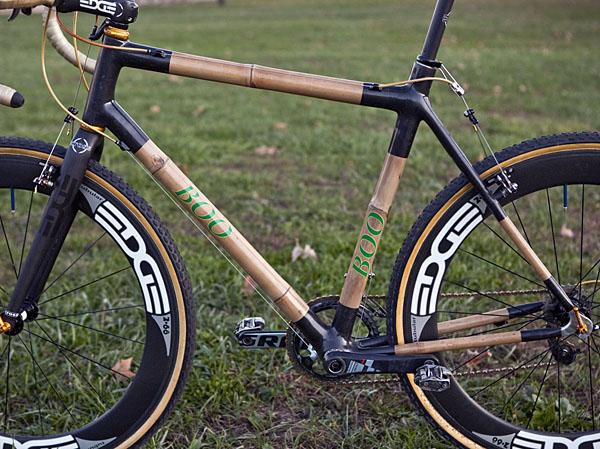
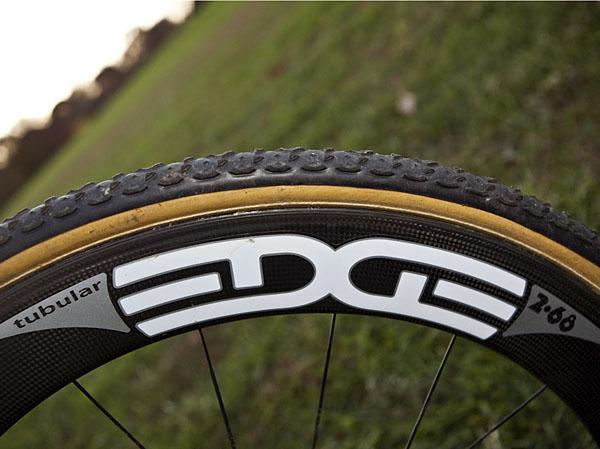
Tyler Wren's Boo Bicycles CX is among scores of composite bicycles currently being raced in the upper tiers of cyclo-cross - only it's not just carbon fibre and actually comprises not one, but two distinct composite materials in its novel construction.
Manmade carbon fibre is used for the joints and short sections of tube but the primary structure is instead provided by Mother Nature: bamboo.
Boo Bicycles creator - and former U23 US national time trial champion - Nick Frey was first attracted to using bamboo as a material for bicycle frames while a student at Princeton University, citing its better vibration-damping capabilities relative to carbon fibre, naturally light and stiff material properties, impressive damage tolerance, and eco-friendly sourcing.
Frey admits that the development process hasn't been easy: bamboo is prone to splitting lengthwise when cured, can be susceptible to weather and insect degradation, and while its sustainable production makes for a good 'green' argument, it also lends unavoidable variation in the raw materials.
But Frey feels he and his development partner in Vietnam have refined process specifics such as drying, aging, butting, and even harvesting timing and plant maturity to where finished products are not only consistent and reliable but can also be tuned based on desired performance characteristics.
"Bamboo is radially symmetrical but it is not symmetrical from inside to outside - its fibre density increases towards the outermost layer of bamboo, because it grows from outside-in (opposite to a hardwood tree)," Frey said. "The outer fibres are the most mature and the stiffest, meaning the tube can be tuned based on how much of the inner fibres we drill out. The tube's outside diameter and wall thickness are chosen based on what tube of the bike it will become as well as what size frame it's going into, and we can custom tune every tube in our full custom bikes based on what type of rider is buying it.
The outer ends of each mitered tube are milled down two milimetres, then hand-wrapped in pre-preg carbon tow, physically compressed with rubber hose (in a process similar to how handlebars are taped), and cured. Final sanding and clearcoating yields aesthetically pleasing flush joints. Though the process sounds like garage-based science on paper, Frey insists that it's anything but and frame construction is done in a properly climate-controlled facility overseas.
The latest race content, interviews, features, reviews and expert buying guides, direct to your inbox!
"The wrapping process is really the only detail I will never speak of; it is a Boo trade secret and we have figured out how to align our fibres in the orientation of the load path for each joint," said Frey. "This drastically increased our frame stiffness (a test T-joint tripled in stiffness compared to our first carbon joints!) and has allowed us to tune our ride properties and focus on reducing frame weight.
"The rubber hose is very pliable and allows for even compression and the joints are allowed to cure before sanding and shaping. Because the top layer is cosmetic, we can sand down the joint and maintain the stiffness because the structural layers remain untouched."
Up front, Frey uses a more conventional aluminum sleeve, fibreglass insulating layer and more hand-wrapped carbon fibre for the straight head tube, and custom CNC machined aluminum dropouts are used out back. Another aluminum sleeve is inserted into the seat tube for a precise fit on the post and a conventional threaded bottom bracket shell is used down below.
Additional 'cross-specific details on Wren's frame include a shaved-down top tube underside for more comfortable shouldering plus removable cable guides to accommodate various drivetrain configurations.
Current claimed frame weight is around 1,800g (3.97lb) and Frey says he hopes to bring that figure down to a more competitive 1,400g in the near future. An upcoming Boo RSL road frame will include carbon sleeves and a carbon BB30 bottom bracket shell developed by Edge Composites but even so, he's quick to point out that ultimate light weight isn't his goal nor ultimate stiffness.
In the case of 'cross, the extra vibration damping and compliance also promotes better tyre traction and a fresher rider towards the end of a race.
"We decided at the outset to have very stiff, durable, long-lasting frames and pare down the weight as we get more experience with the build process and more time to test frames," Frey said. I believe that it is very important to have a frame that will survive crashes rather than a race day-only bike that cracks easily."
Work in progress or not, fellow Princeton graduate Wren - who also rides on the road for Jamis-Sutter Home p/b Colavita - has already enjoyed some success on the prototype BooCX Frey supplied to him, including a 10th-place finish at the UCI C2 'cross race in Wissahickon, Pennsylvania earlier this season.
Built up with an array of premium componentry including SRAM Red/Force, TRP EuroX brakes, and a gamut of carbon goodies from Edge Composites, total weight is a reasonable 8.07kg (17.8lb). "The coolest part of this crazy bike is that it totally works," said Wren. "It's not a boutique showroom-only frame. Bamboo is an ideal material for cyclo-cross and there is no down side here, no compromise for its beauty and uniqueness.
"I was a bit worried about its durability at first, given the unusual material and the light frame weight," he continued. "I've crashed the rig already and chipped the bamboo, which probably would have cracked a carbon frame and dented an aluminum frame, but this material is strong enough to take repeated impact and retain its integrity."
Bike specifications
Frame: Boo Bicycles CX
Fork: Edge Composites Cross
Headset: Chris King NoThreadset
Stem: Edge Composites carbon, 11cm x -6°
Handlebars: Edge Composites carbon, 44cm (c-c)
Tape/grips: Deda Elementi
Front brake: TRP EuroX
Rear brake: TRP EuroX
Brake levers: SRAM Red DoubleTap
Front derailleur: SRAM Force
Rear derailleur: SRAM Red
Shift levers: SRAM Red DoubleTap
Cassette: Shimano Ultegra CS-6600, 12-25T
Chain: KMC X10SL
Crankset: SRAM Red, 172.5mm, 39/46T
Bottom bracket: SRAM Red GXP
Pedals: Time ATAC Alium
Wheelset: Edge Composites 2.68 tubular
Rims: Edge Composites 2.28 tubular
Front hub: DT Swiss 240s
Rear hub: DT Swiss 240s
Spokes: DT Swiss Aerolite
Front tyre: Challenge Fango tubular, 32mm
Rear tyre: Challenge Fango tubular, 32mm
Saddle: fi'zi:k Aliante k:ium
Seat post: Edge Composites carbon
Bottle cages: n/a
Computer: n/a
Other accessories: KCNC QR skewers and seatpost clamp, Jagwire cable and housing, Hudz brake hoods
Critical measurements
Rider's height: 1.8m (5' 11")
Rider's weight: 64.9kg (143lb)
Saddle height, from BB (c-t): 785mm
Saddle setback: 70mm
Seat tube length, c-t: 580mm
Seat tube length, c-c: 510mm
Tip of saddle nose to C of bars (next to stem): 550mm
Centre of front hub to top of bars: 590mm
Head tube length: 160mm
Top tube length: 573mm
Total bicycle weight: 8.07kg (17.8lb)