Inside: Bontrager's Wisconsin wheel factory
The people, machines and custom tools behind Trek's wheels
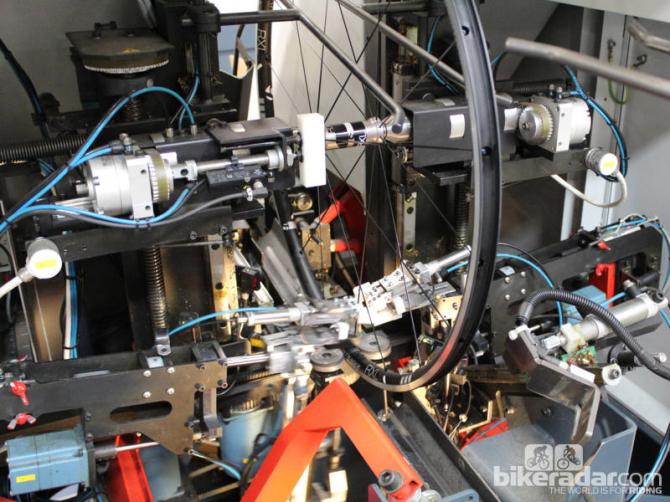
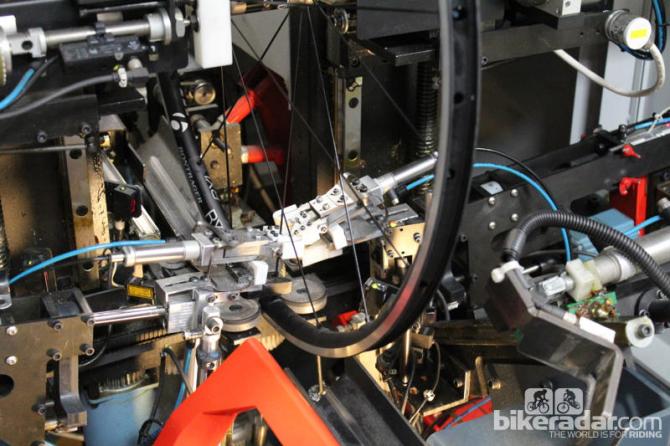
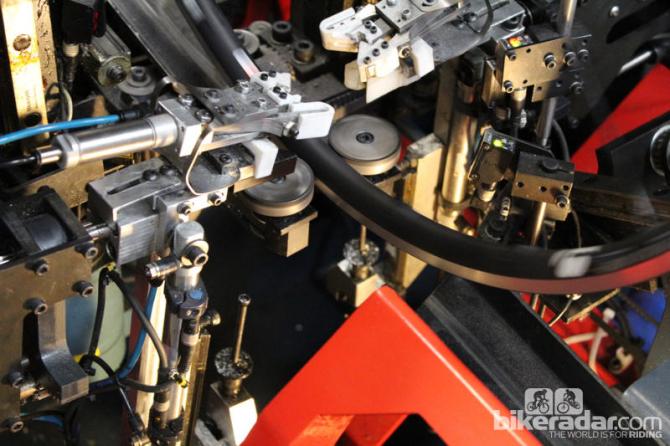
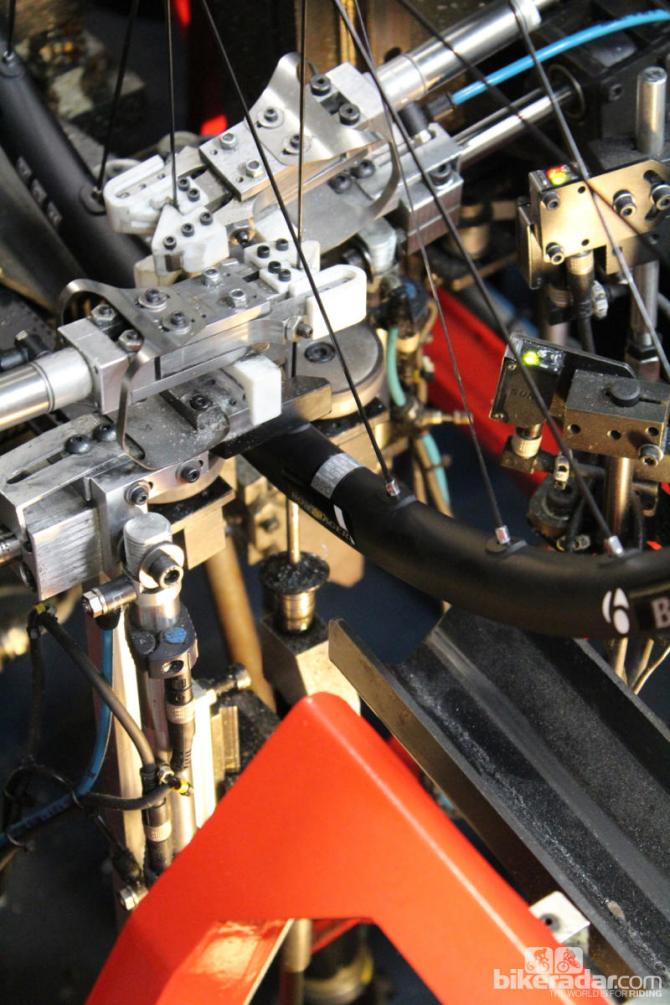
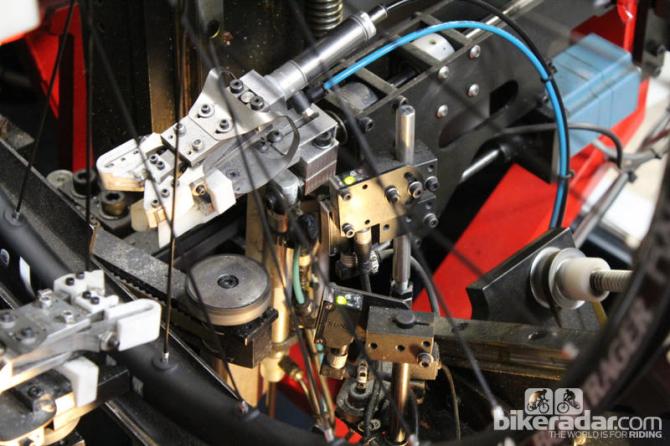
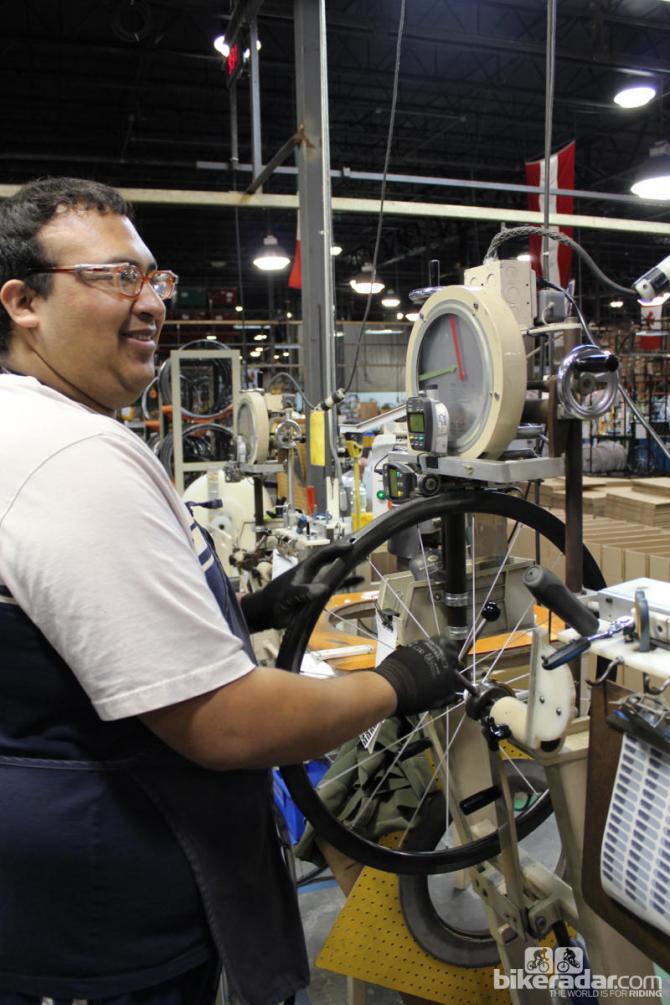
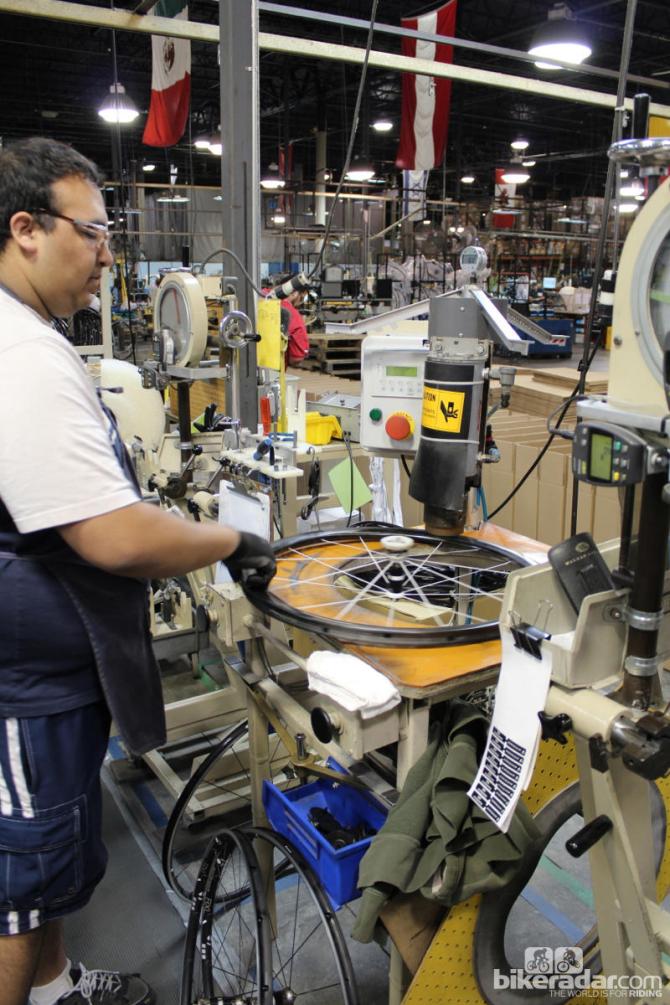
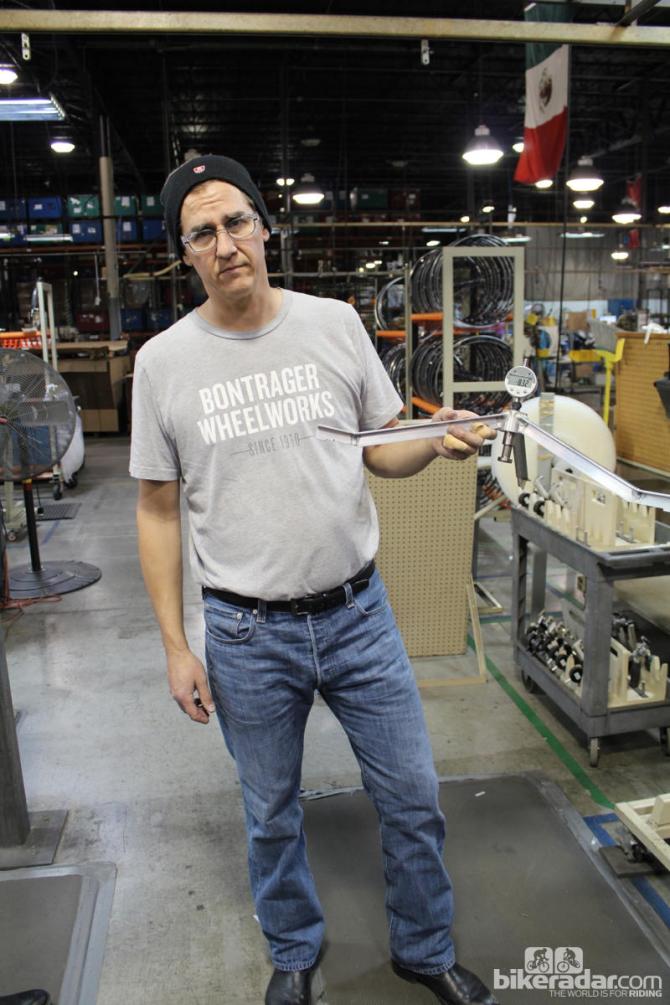
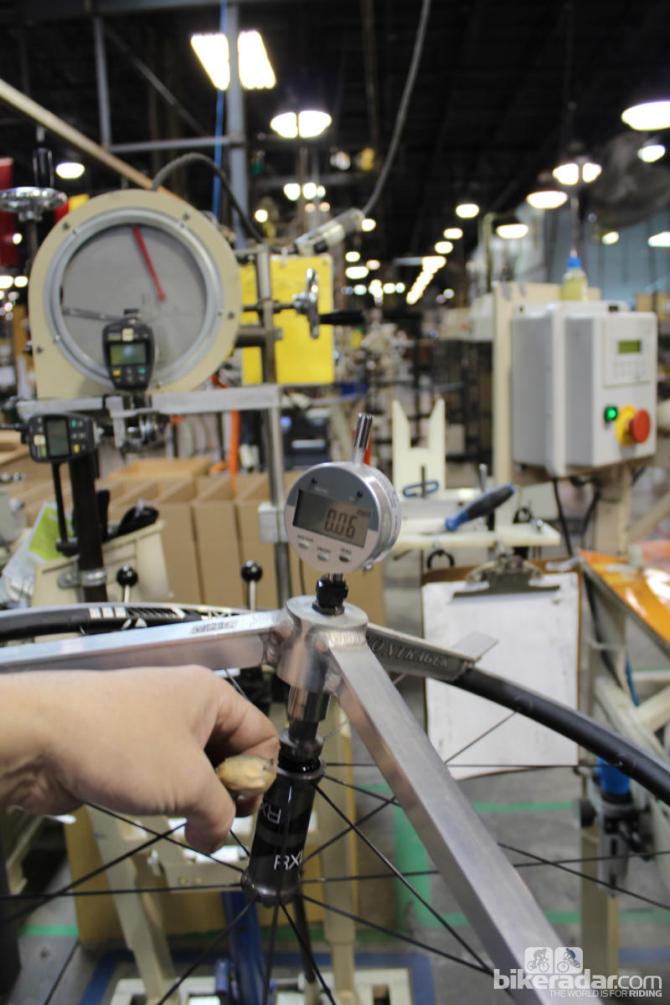
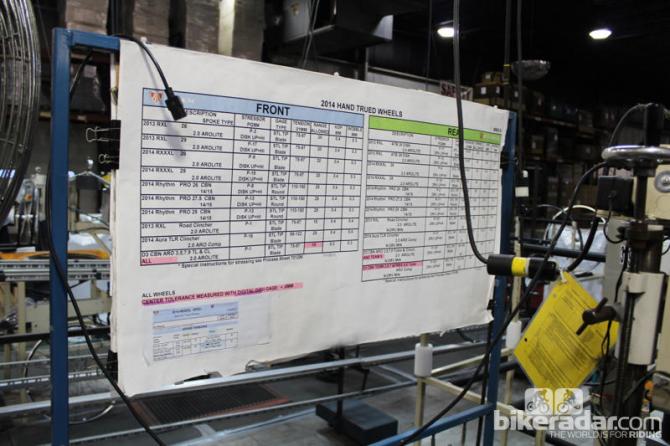
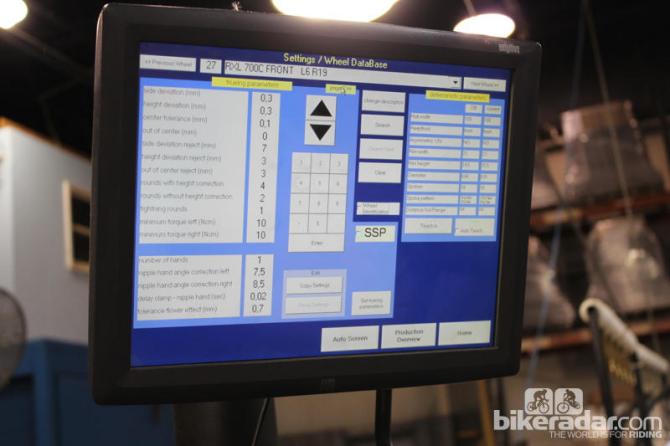
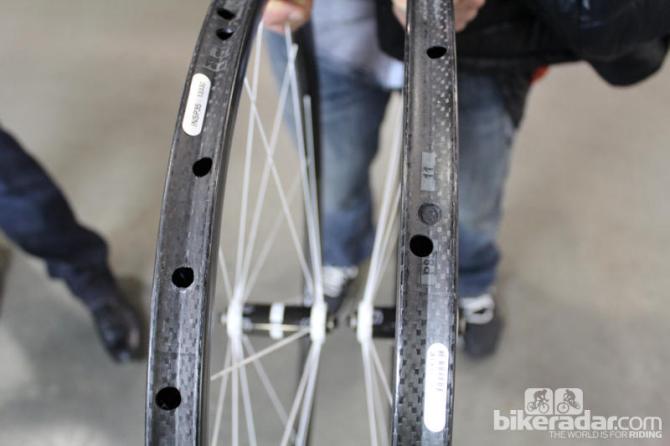
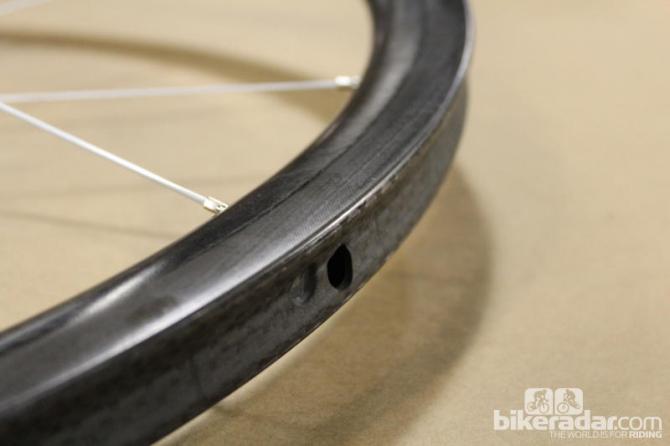
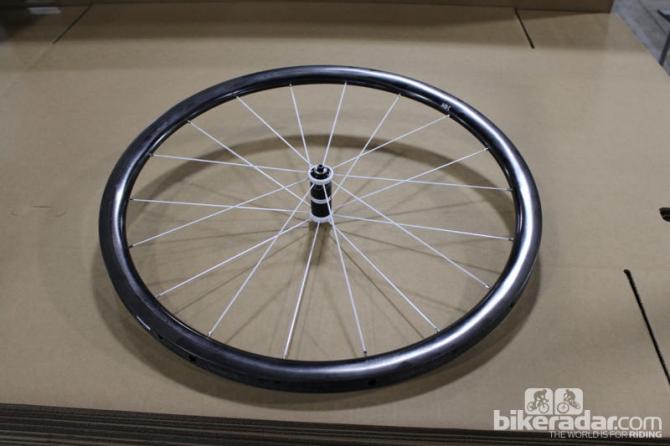
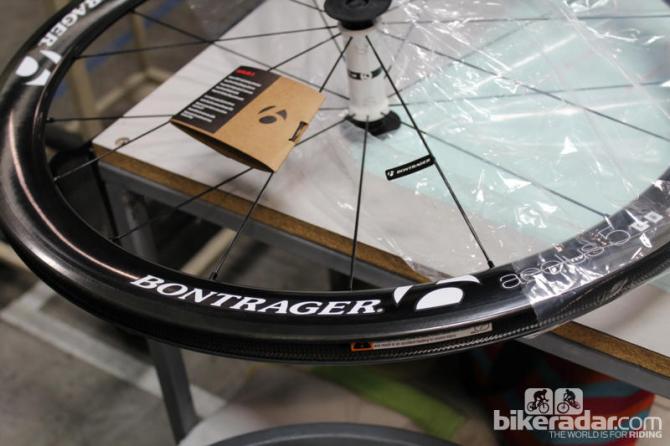
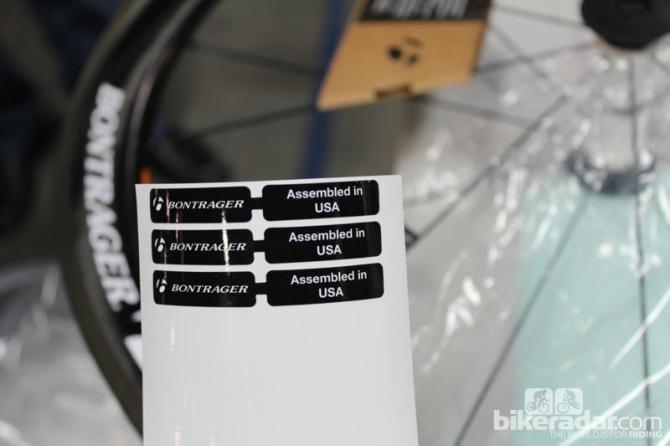
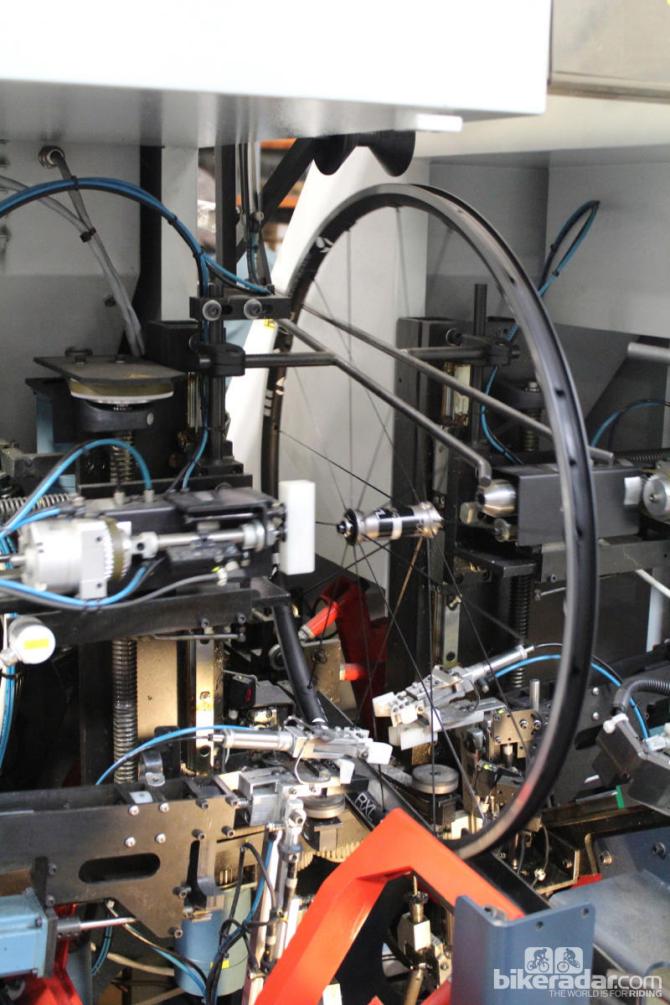
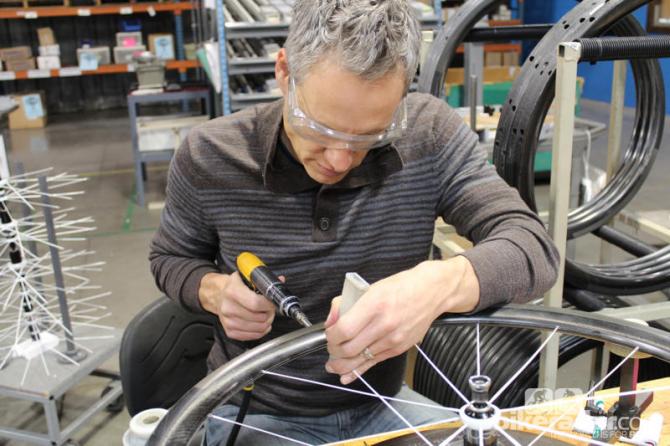
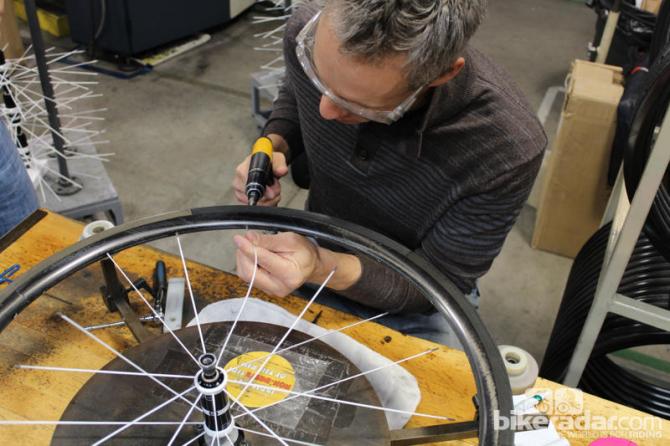
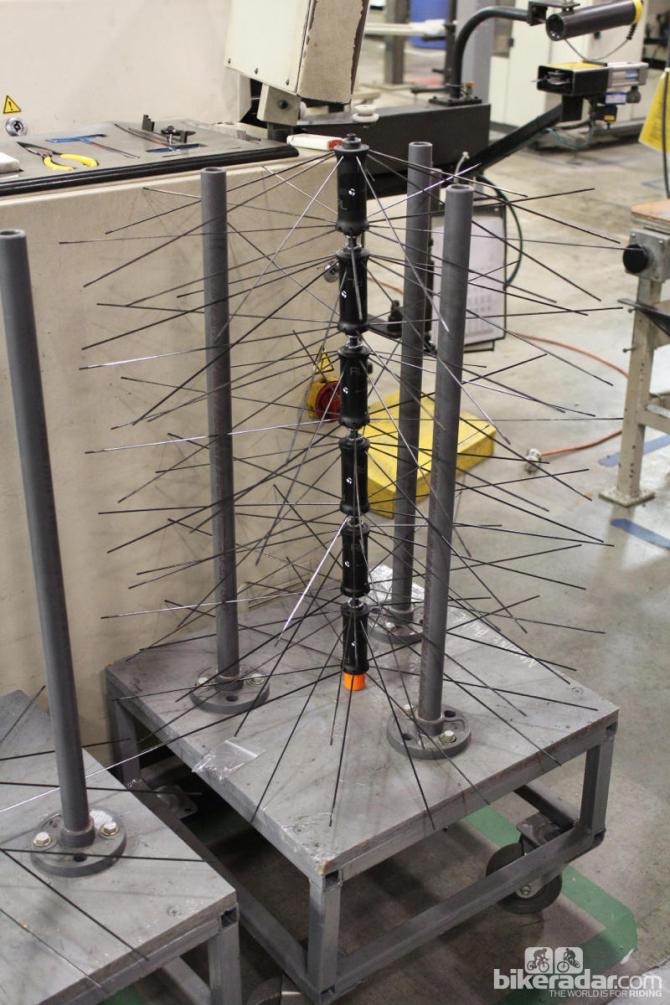
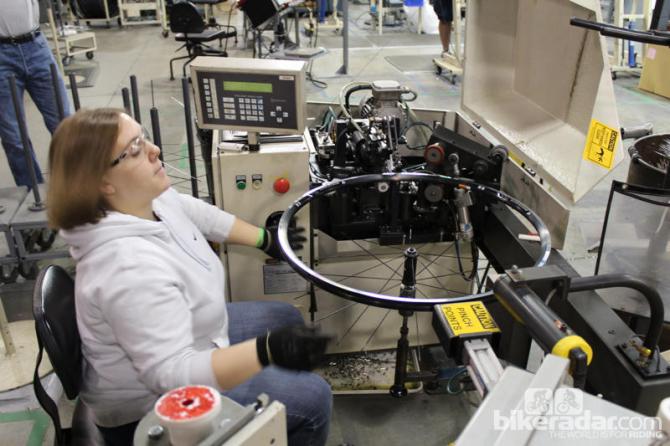
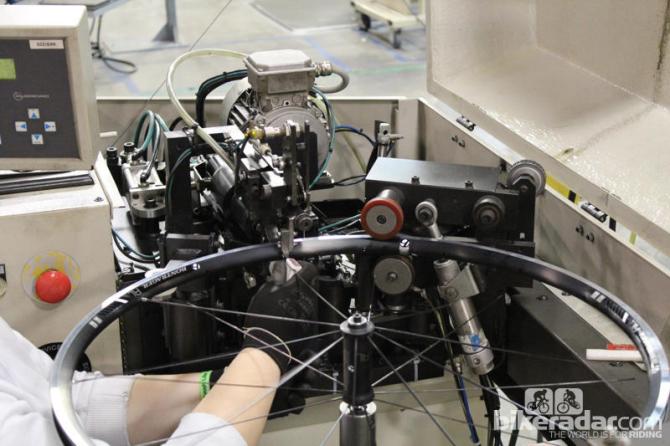
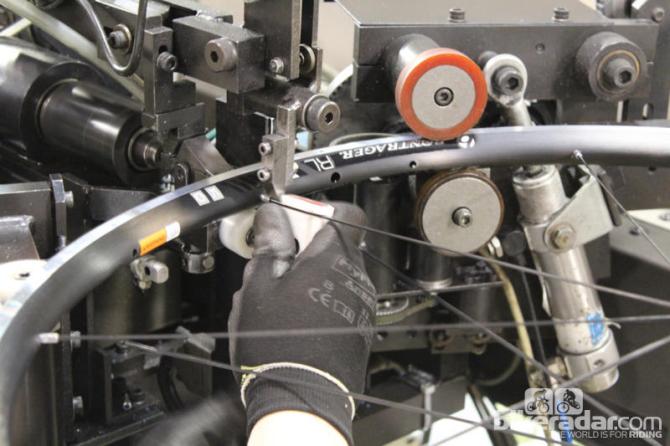
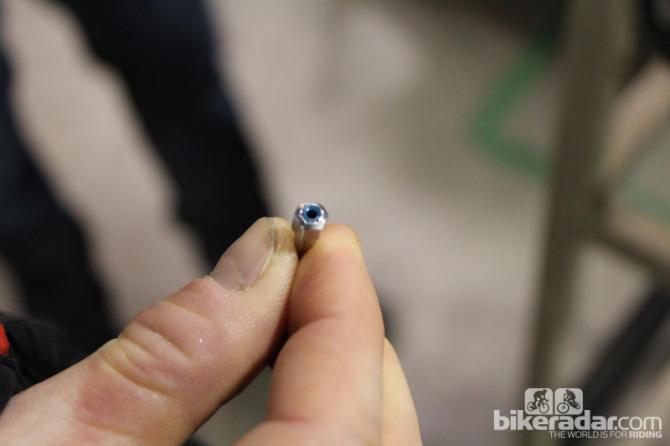
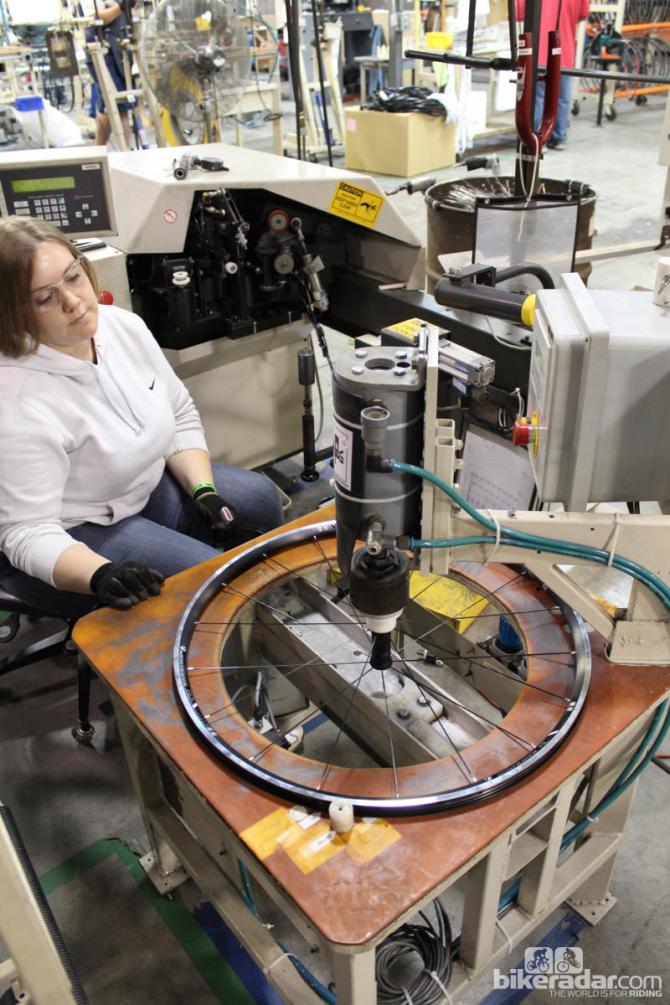
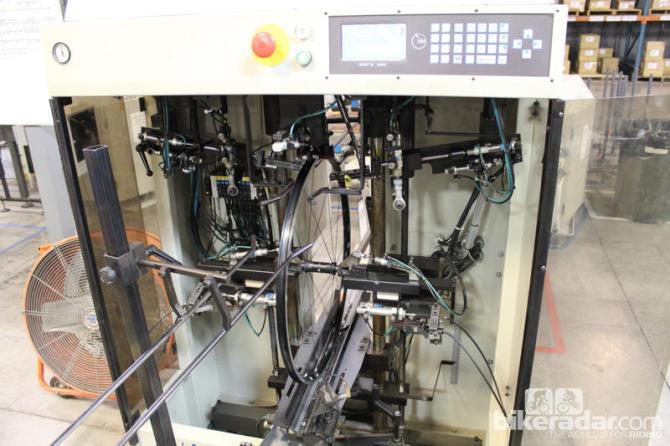
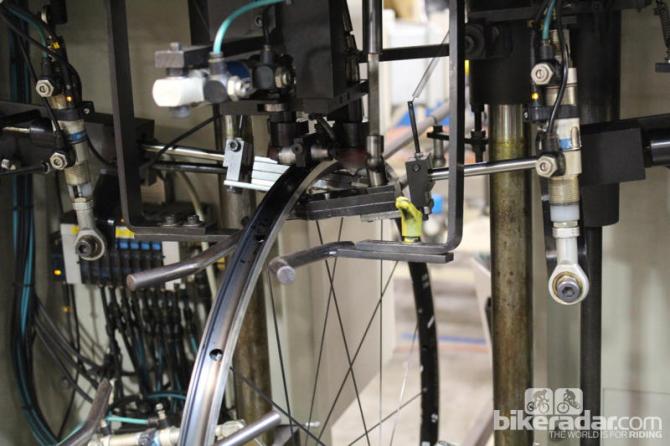
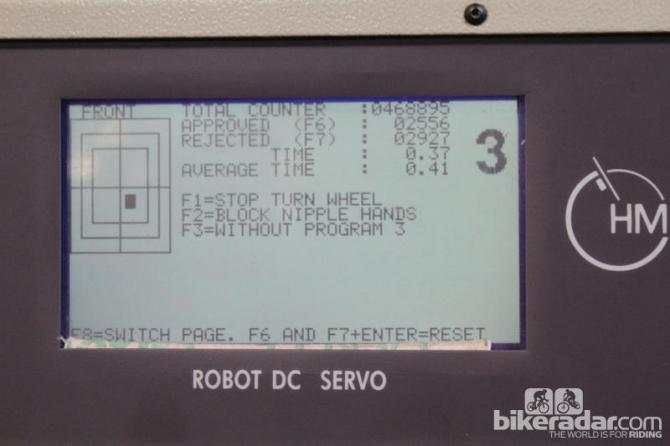
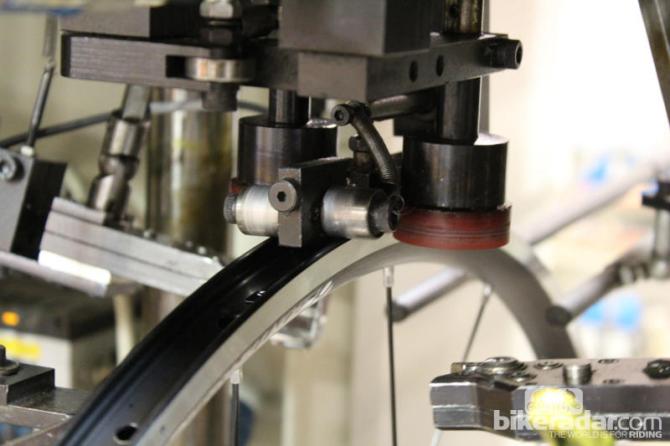
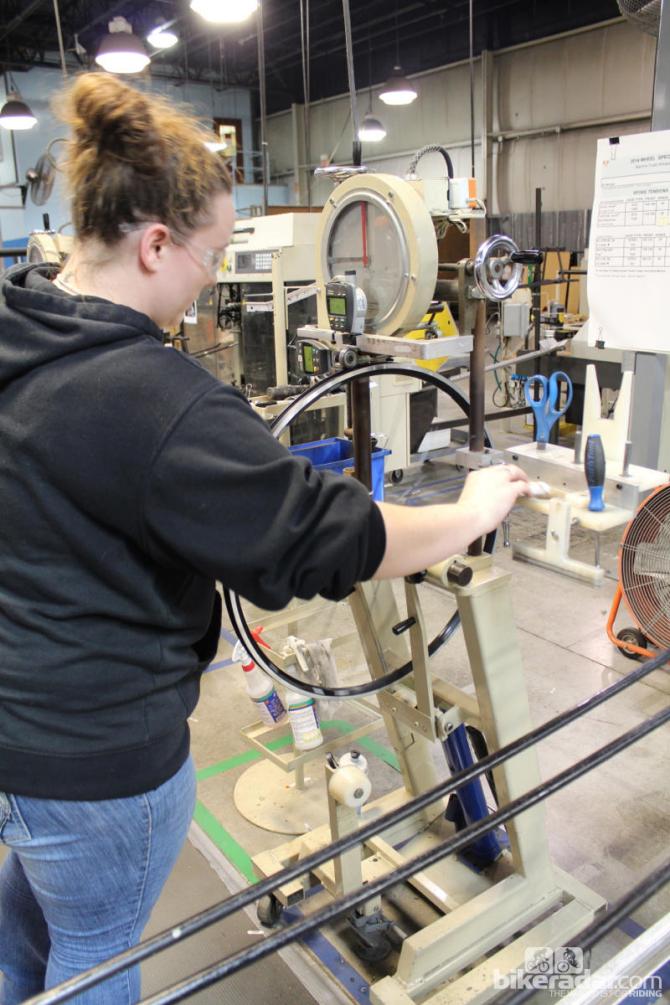
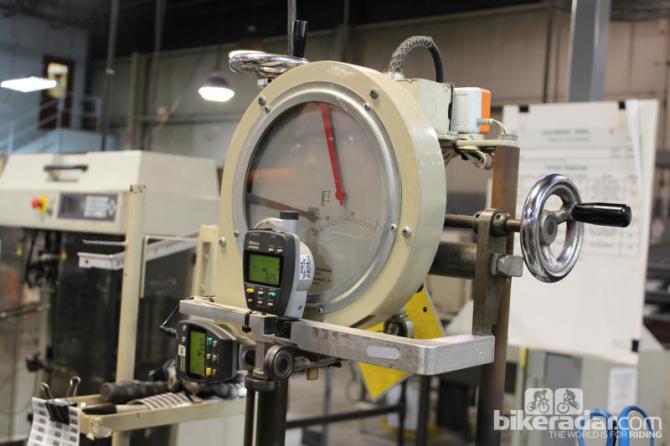
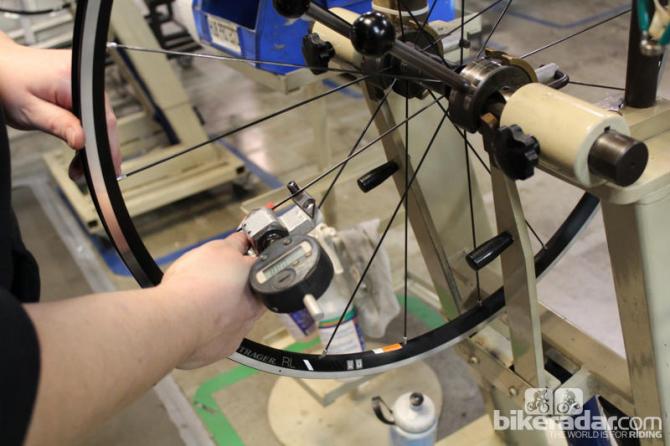
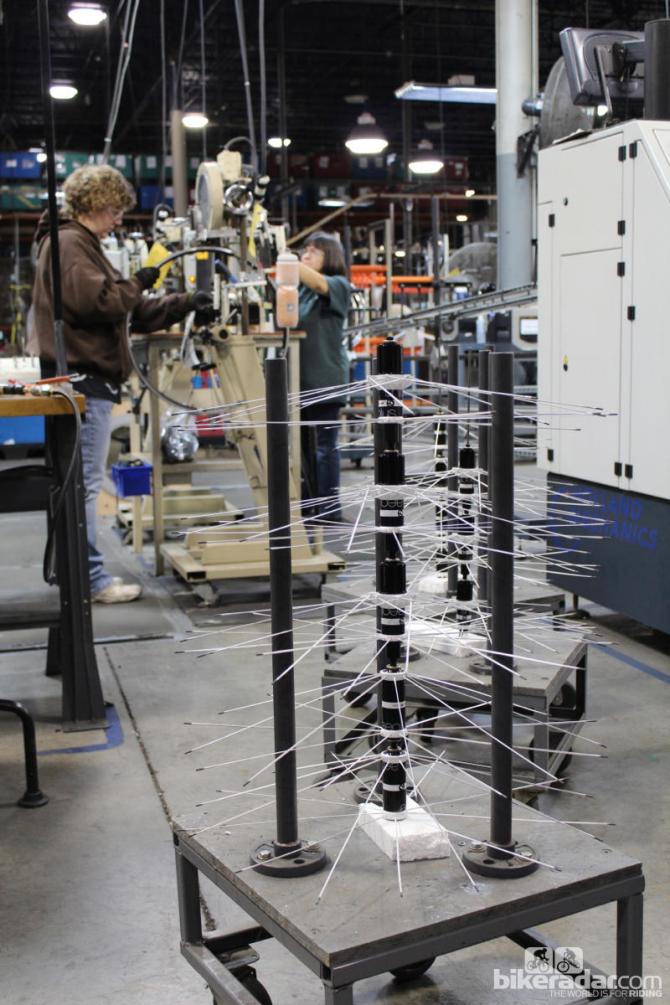
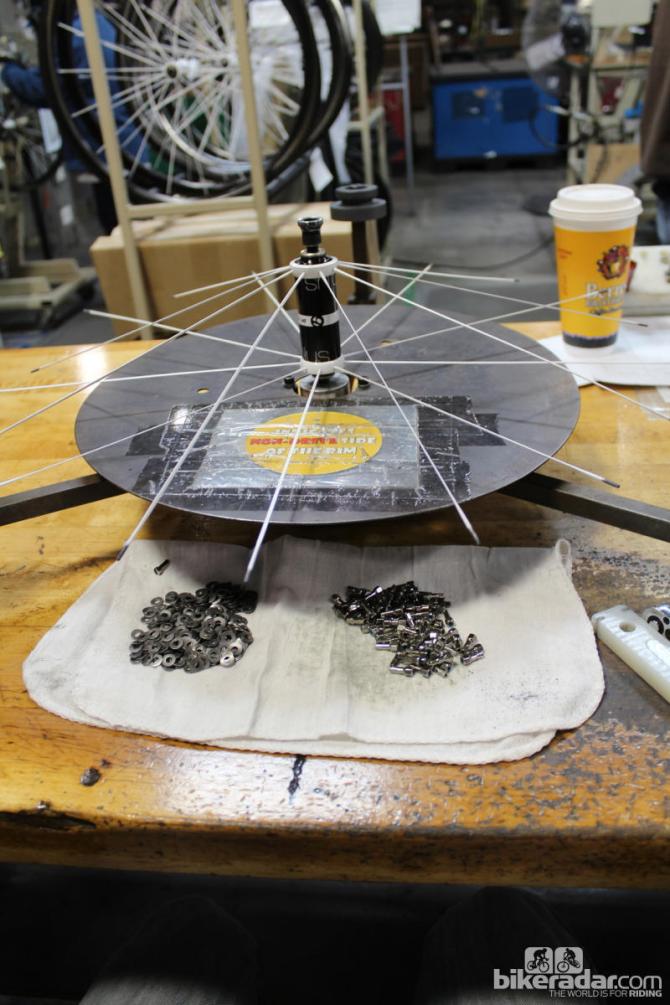
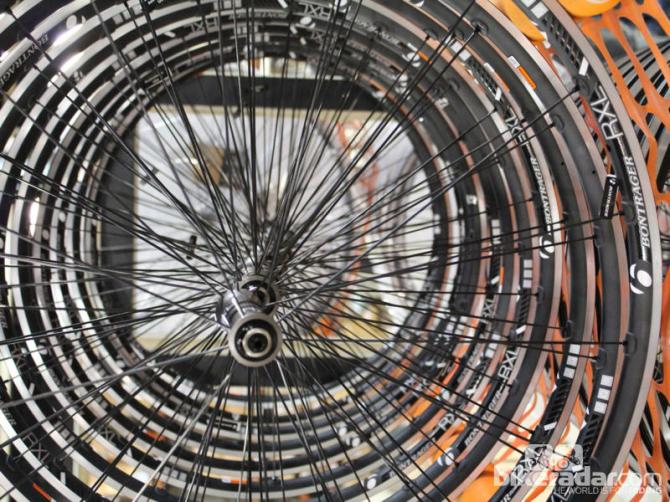
This article originally published on BikeRadar
Inside a cavernous warehouse that used to employ 500 people when Trek was manufacturing steel bikes in Whitewater, Wisconsin - today a dozen builders lace up Bontrager wheels for pro teams and consumers, while another team nearby assembles Project One bikes to customers' individual specifications.
Located about an hour's drive east of Trek's headquarters in Waterloo, Wisconsin, the Bontrager wheel facility can build up about 80 pairs of handbuilt or 200 pairs of mostly machine-built wheels a day. When BikeRadar visited in early December, Bontrager was assembling hundreds of wheels for the ProTour team they sponsor. Among the many models built for the team is an extra-wide tubular called the Race Shop Limited, referred to internally as 'the Roubaix wheel' as it is intended for the brutally tough race, Paris-Roubaix. Built with a shallow, almost flat tire bed, the rim is a variation of the Bontrager D3, a 35mm tall rim with an aero profile. The rim is so wide and shallow that it requires a minimum tire width of 27mm.
There are still a few hundred bikes moving through the building, but they are all Project One models, where customers get to pick the parts and graphic design, as well as add their names or small sayings to the frame. The Project One frames are built, painted and decal'ed at Trek's headquarters in Waterloo, then trucked here for assembly. Massive aisles with towering shelving house deep inventory for high-end parts. The end result: the Whitewater facility can build and ship a Project One bike in under two days.
Trek builds 1.5 million bikes a year worldwide, according to spokesman Michael Browne. Project One bikes account for well under a percent of that total. Still, the change from shipping bikes en masse out of Whitewater to one at a time has caused the company to completely rework its logistics, said Matt Vos, an 18-year veteran with the company. "When I started, we were shipping 300 bikes at a time. Now we do a handful of bikes a day — but every one is unique," he said.
Not every one of Bontrager's wheels coming out of Whitewater is unique, but the team does have some custom tools and individual build specs for each type of wheel. Bontrager sources its aluminum rims from Taiwan, but its carbon rims come from closer to home: Zipp builds carbon-clincher rims to Bontrager specs in Indiana, and Trek builds carbon-tubular rims at HQ in Waterloo.
Jef Bogstad, Bontrager's manufacturing engineer and another 18-year veteran with company, walked us through the Bontrager wheelbuilding process.
The latest race content, interviews, features, reviews and expert buying guides, direct to your inbox!
Wheelbuilding in Whitewater
There are five basic steps to Bontrager's wheel assembly process:
1. Lacing
2. Stressing
3. Truing
4. Digital check
5. Sticker and package
Bontrager has two basic assembly methods; mid-range wheels are laced and largely trued by a machine, while the higher-end wheels are laced by hand then initially trued by a machine, with steps 2 and 3 often repeated by hand until the wheel is within the required spec.
To lace the wheels, a wheelbuilder first preps hubs in batches by threading in spokes.
Next, the wheelbuilder then connects nipples either with a machine or by hand with a pneumatic drill. In both cases, the nipple is inserted through the back of the rim, and spokes are connected by alternating pairs, slowly building up tension on the wheel.
After all the spokes are connected, the wheelbuilder stresses the wheel by loading the wheel laterally at the hub, one side at a time.
"We custom stress each type of wheel," Bogstad said. "We calculate the stress for each wheel, taking into account the spoke count, lacing pattern and which side of the wheel it is. For example, a disc brake wheel has different stress when on the bike, so we load to 300 pounds on a carbon wheel on the non-disc side, and 550 pounds on the rotor side. We don't have 'one size fits all' solutions for anything."
Stressing the wheel force everything to settle in - the spokes, washers and nipples.
Then the wheels are fed into one of two Holland Mechanics wheelbuilding machines, one of which has been with the company as long as Bogstad has. Rotating the wheel while measuring for trueness and hop, the machine quickly tightens each nipple.
Hop is measured at the rim with two little rollers on the older machine, and with a stack of LEDs on the newer machine. Trueness is measured in both machines, almost counter-intuitively, at the hub; software makes the necessary adjustments at the nipple in the rim as the machine turns the wheel.
The newer Holland Mechanics machine can even adjust truing of the wheel to minor eccentricities of a hub. "Not that these high-end hubs have eccentricities, but it's pretty cool that the machine has that level of resolution," Bogstad said. "We can get a wheel within half a millimeter in the truing machine."
Another benefit of the new machine is for cosmetics. Since it trues the wheel through the rim with a pair of angled 5.5mm hex heads, the nipples and the rims are not scuffed — a definite bonus when Bontrager builds with white spokes.
Once the high-end wheels come out of the truing machine, they are stressed and hand trued, and then re-stressed and hand trued until nearly perfect. "The machine doesn't do everything, but it does give the wheelbuilder a really, really good start," he said.
The other wheels also get a once-over by hand in a Villum wheel stand to check for spoke tension, dish and trueness - and are adjusted as necessary.
The final checks are done with digital tools, including one made in house: a three-legged dish gauge.
"A lot of this stuff comes about from disputes. One inspector will say a wheel is out of spec, another will say it is in spec - and both were pointing to tools," Bogstad said. "So we developed better tools to measure that. It is the same with digital gauges. The mechanical gauges on the truing machine are great for quick visual checks, but one gauge would differ from the next."
Once everything is confirmed to be up to snuff, the wheels are stickered, bagged and boxed for distribution.
Click through the photo gallery for a more detailed look at Bontrager's wheelbuilding process.